You may have heard multiple references to ‘Industry 4.0’ previously, with many presenting this as a technological revolution that will ultimately cost human jobs and fundamentally change the global workplace for the worse. As a matter of fact, the Industry 4.0 will transform the workforce of today and create many new and highly lucrative career opportunities. But training for them is key. Industry 4.0 comprises several disruptive technologies that together help revolutionize how companies automate, manufacture, and distribute their products efficiently. It is widely misunderstood and underestimated in terms of the new and more skilled jobs that it can create.
This is evident in skilled trades such as welding, which is a key component of various industries including aerospace and automotive manufacturing. In these instances, innovations like artificial intelligence (AI) continue to drive automation and eliminate manual tasks, while creating a need for higher-skilled labor to monitor robotic systems and manage output efficiently. In this article we will explore the welding industry and the role of robotics in more detail, and how they can help react to future changes in the market.
The Welding Industry – A Brief Exploration
Overall, the automation of manufacturing and tasks such as welding is central to the Industry 4.0 proposal, with the deployment of automated tasks in factories set to increase from 5% to 8% by the year 2028 as the industrial landscape continues to change on a large scale. In addition to undergoing a significant evolution in terms of how manual welding tasks are undertaken, this industry is also experiencing a global shortage of workers that remains far below the existing demand.
To provide some context, the global demand for welders is increasing by 8% annually, but the National Association of Manufacturers (NAM) has reported that close to 81% of manufacturers in the US alone cannot find enough skilled welders to meet their needs. The American Welding Society has also predicted a deficit of 400,000 welders by the year 2024, with this having increased over 30%, from a shortage of approximately 290,000 welders in 2020.
But what is behind this imbalance between supply and demand? In truth, there are several factors, including the average age of existing skilled welders is over 50 years of age and that many are approaching retirement without a new generation of skilled welders to replace them. It is estimated that the average age of a welder is 57 years, with the number of those leaving the industry continuing to outstrip the influx of new talent every single year. At the same time, traditional welding training is failing to attract the attention of younger applicants, creating a situation that continues to be exacerbated over time.
Despite the increased sophistication of welding applications and the fact that skilled welders can now attract an annual salary more than $100,000, recruiters are struggling to identify talent and meet demand. These challenges, coupled with the impact of disruptive technologies and increased use of robotic welding systems, are continuing to drive widespread changes in the industry and create a pressing need for efficient, tech-led solutions.
What are the Benefits of Robotic Welding Training?
Interestingly, one of the most effective solutions could be the training for robotic welding. In simple terms, this comprehensive process provides detailed insight into the use of robots, from their initial programming to the detailed analysis of the finished weld bead and across a broad range of industrial applications.
Despite this, the industrial welding sector is continuing to grow at a much faster rate than education in robotics training, creating a scenario where the market is evolving quicker than the skillsets of the workforce and compounding the global welder shortage. This is where robotic welding training enters the race. This incredibly emerging market offers a huge opportunity for training providers and industrial welding, as it resolves many of the challenges associated with welding applications across the globe.
- Increase Cycle Times and Productivity: Using automated welding robots, factories can introduce quicker and more consistent cycle times. This is largely because robotic welding systems can be utilized 24/7, or on flexible schedules depending on output and supervision capacity.
- Improve Productivity and Reduce Injury: This increase in speed does not come at the expense of productivity or precision when using robotic welding systems, which is a huge boon to manufacturers. Increased productivity can also be achieved while minimizing the risk of injury and welding staff undertake safer and less hands-on roles.
- Create More Consistent, Higher Quality Welds: One of the main advantages of robotic welding systems is its ability to drive more consistent and higher quality welds. This is because programmable robots help to systemize the use of materials and workflow, allowing the robot to operate at optimal efficiency.
- Reduced Waste and Less Rework: Over welding is a key issue in any industry, particularly in terms of the drain that it places on your company’s time and financial resources. Robots work to ultra-precise and pre-programmed specifications, however, with a view to negating human error and minimizing waste.
- Minimize the Post-Weld Cleanup: While you may not be able to completely eradicate mess or waste during welding projects, this can be dramatically reduced using robotic systems. It certainly minimizes weld splattering and other mess, reducing the need to clean up and the time that elapses between projects.
With these benefits in mind, it is easy to see why the global robotic welding market is set to achieve a cumulative market value of $10.784 billion by 2026. Over the course of the next four years, it will grow at a CAGR of 8.7%, as this thriving market continues to benefit from technological advancement. Manufacturing automation provides the backbone of Industry 4.0 and its disruptive technologies, which primarily work to automate tasks like welding and impact how projects are delivered.
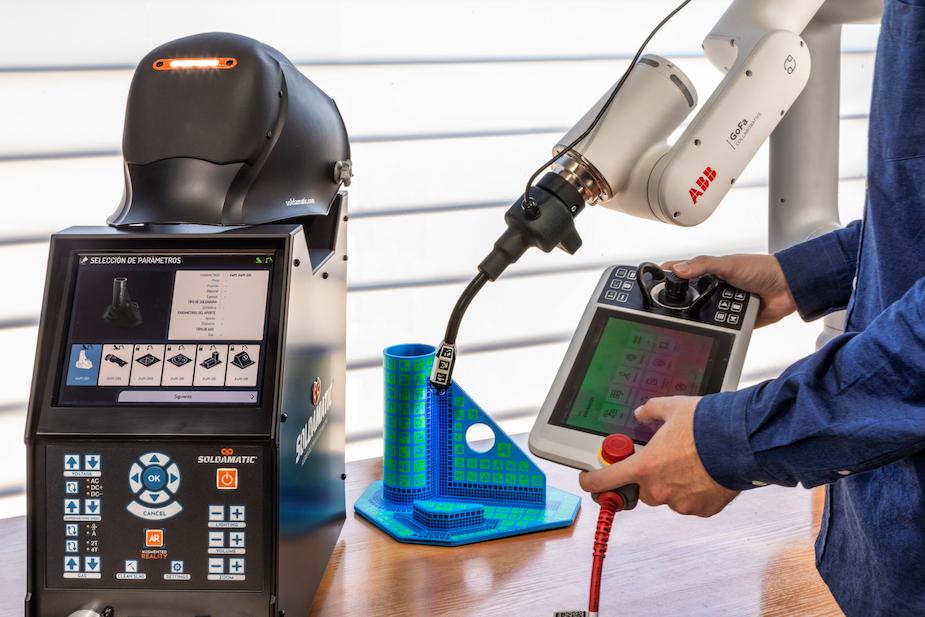
While this removes traditional welding jobs as we recognize them, it also creates the need for a much higher skilled workforce that can operate welding robots, monitor their performance, and manage output daily. In this respect, robotic welding systems are ‘cobots’, or collaborative robots that require continual interaction with humans and potentially create better paid opportunities across all welding applications.
The good news is that robotic welding training can help to impart new and relevant skillsets to both new and existing workers. It also provides retraining to welders whose jobs may have been lost to automation (in addition to incentivizing a new demographic of workers), creating a better balance between supply and demand in the global workforce.
Soldamatic Robotics – What do you need to know?
Through Soldamatic’s patented and state-of-the-art robotic welding training, you can combine Augmented Reality simulation (powered with HyperReal-SIM) with the use of customizable and scalable robot hardware. This creates completely immersive and realistic training scenarios, ensuring that highly relevant skills are taught as efficiently as possible.
Soldamatic Robotics is beneficial to the wider market because…
1) It is Comprehensive and Customizable: The flexible solution features multiple industrial teach pendant settings when combined with Seabery’s patented software. Soldamatic Robotics allows for remote control across a range of professional, educational, and manufacturing applications. This offers access to a comprehensive curriculum with hundreds of built-in capabilities and opportunities.
2) It is Scalable: Soldamatic’s software also offers a scalable training solution that can be adapted to suit any type of industrial or educational institution. In fact, users can access to a wide catalogue of welding joints for multiple positions, while training can also be delivered in classrooms or on-the-job as required.
3) It is Accessible: You can also access to Soldamatic Robotics welding training from anywhere and at any time, while it is possible for users to enjoy unlimited practice and simulations. It can also be easily integrated into an existing curriculum and learning environment, thanks largely to the fact that it is modular, open, and incredibly simple to use.
4) Impart Both Practical and Theoretical Knowledge: Using a Robotics license that allows communication between the software and the robot, trainers can create custom-made courses and practical exercises, and access multiple datasets when evaluating the results. This also enables beginners to follow both theoretical and practical topics, including specific robot welding content.
These benefits highlight the unique appeal of Soldamatic Robotics welding training in the digital age, particularly at a time where robotics and automation has begun to revolutionize manufacturing and industrial applications.
Soldamatic Robotics offers training that is relevant and far more engaging for younger applicants, creating immersive learning that unlocks increasingly viable skills for the future workforce. This helps potential graduates and the next generation of welders to reimagine a trade that is largely seen as outdated, while ensuring that they can access realistic, simulated training, which, at the same time, awakens interest and encourages greater knowledge retention.
Welders and Robotics: The perfect match!
Since 2009, the use of manufacturing robots has more than doubled, while this is set to grow by a further 80% by 2026. This is fundamental to the Industry 4.0 revolution, which will seek to automate manufacturing processes while creating higher-skilled and more senior supervisory jobs in the process.
Clearly, robotic welding training provides a clear opportunity to aid workplace transition, while also resolving other issues such as the global shortage of welders and the lack of appeal of tasks like welding among younger candidates. By understanding robotics and embracing its underlying technologies, both wider industrial companies and educational institutions can cope more effectively with change and create a new generation of workers with tailored and relevant skills.
In this respect, Soldamatic Robotics is at the forefront of positive change and evolution across a broad range of industrial applications, so get in touch with Seabery today to learn more about our solutions and how they can benefit you.