Welding is a vital technique used in various industries to join metal parts permanently. From constructing skyscrapers to manufacturing intricate machinery, welding plays a crucial role in creating durable and structurally sound products. However, there is not just one welding process. In fact, there are several methods, each with its own set of characteristics and applications. In this blog post, we will explore the main types of welding processes, providing an explanation of each and highlighting their key features.
What are the main types of Welding processes?
Shielded Metal Arc Welding (SMAW)
Shielded Metal Arc Welding, commonly known as stick welding, is one of the oldest and most versatile welding processes. It involves the use of a consumable electrode covered in a flux coating. The electric arc generated between the electrode and the workpiece melts the metal, and the flux coating releases gases to shield the weld pool from atmospheric contamination. SMAW is widely used in construction, maintenance, and repair work due to its portability and ability to work in various environments.
Gas Metal Arc Welding (GMAW)
Gas Metal Arc Welding, also known as MIG (Metal Inert Gas) welding, is a popular choice for both industrial and DIY applications. In this process, a continuous wire electrode is fed through a welding gun, while a shielding gas, typically a mixture of argon and carbon dioxide, protects the weld zone. GMAW offers high welding speeds, excellent control, and can be used to weld various metals, including steel, aluminum, and stainless steel. Among the various welding processes, this particular one enjoys the highest popularity within the construction and automotive industries.
Gas Tungsten Arc Welding (GTAW)
Gas Tungsten Arc Welding, commonly referred to as TIG (Tungsten Inert Gas) welding, is widely regarded as one of the most precise and clean welding processes. It utilizes a non-consumable tungsten electrode to create the arc, and a separate filler metal is manually added, if necessary. GTAW produces high-quality welds with exceptional aesthetic appeal and is frequently used for critical applications in industries such as aerospace, automotive, and artwork fabrication.
Flux-Cored Arc Welding (FCAW)
Flux-Cored Arc Welding is a versatile process that combines elements of both SMAW and GMAW. It employs a tubular wire electrode filled with flux, eliminating the need for an external shielding gas. FCAW is highly productive, capable of welding thicker materials, and performs well in outdoor or windy conditions. It finds applications in shipbuilding, construction, and heavy fabrication industries.
Submerged Arc Welding (SAW)
Submerged Arc Welding is a high-productivity process that involves the formation of an arc between a continuously fed wire electrode and the workpiece. The arc is submerged under a layer of granular flux, which protects the weld pool and minimizes spatter. SAW is primarily used for welding thick sections of steel in industries such as shipbuilding, pressure vessel manufacturing, and pipe welding.
But how long does it take to learn these types of welding?
According to a study from New England Institute of Technology, there are some differences to highlight between the 4 main welding processes.
- Gas Metal Arc Welding (GMAW) is considered to be one of the most accessible welding techniques to acquire, making it an excellent focal point for novice welders. Additionally, it requires minimal post-weld cleanup, provides fast welding speeds, and allows for superior control when working with thinner materials.
- FCAW Welding is recognized for its affordability and ease of mastery, this welding technique is similar to the MIG welding process, making it an ideal starting point for aspiring welders embarking on their careers in the field.
- Unlike other types of welding, SMAW welding eliminates the need for shielding gas and permits outdoor execution even in adverse weather conditions such as wind or rain. It also demonstrates proficiency when working with dirty or rusted materials. Nevertheless, it is important to acknowledge that certain drawbacks accompany this approach.
- TIG Welding is regarded as one of the most challenging welding techniques to master. This type of welding yields exceptionally high-quality welds.
How can Soldamatic help to avoid those limitations
Welding involves inherent risks, including exposure to heat, sparks, and hazardous fumes. By using Soldamatic welding training reduces the exposure to these risks, ensuring a safe learning environment. Trainees can make mistakes without the danger of injury, and instructors can closely monitor and guide their progress.
Traditional welding training can also be expensive due to the need for materials, equipment, and dedicated training facilities. Soldamatic significantly reduces these costs by eliminating the need for physical resources. Trainees can practice welding virtually, saving on material costs and minimizing the wear and tear on real equipment.
The system provides interactive training modules and exercises that allow welders to develop and refine their skills. They can practice welding techniques, learn different types of welds, and gain proficiency in a controlled and safe environment.
Soldamatic offers real-time feedback and performance analysis, helping welders identify and correct errors, ultimately improving their welding capabilities.
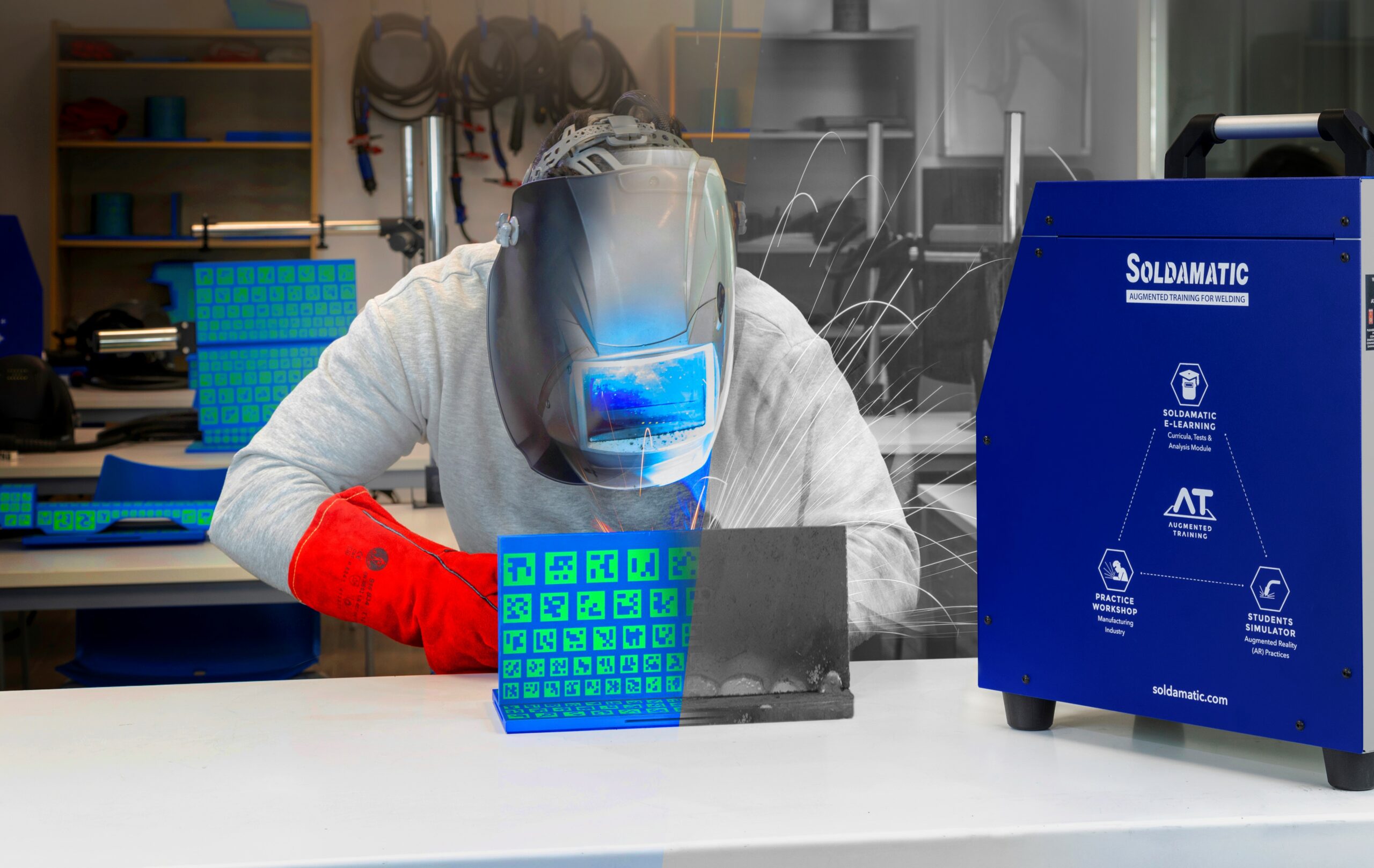
The Last Word
Understanding the main welding processes and their applications is essential for both professionals and enthusiasts in the welding industry. Whether you are considering a career in welding or simply interested in learning more, familiarizing yourself with these processes will broaden your knowledge and help you make informed decisions when selecting the appropriate method for your specific welding needs.
Remember, each type of welding has its advantages and limitations, and further research and practice are key to mastering them. So, dive into the resources provided and explore the fascinating world of welding!