Improving your welding technique is essential for ensuring high-quality welds, enhancing safety, and increasing productivity. By focusing on key areas such as equipment familiarity, technique refinement, and embracing modern technologies, you can elevate your welding skills to a professional level.
Here are five tips to help you improve your welding technique:
1. Master the fundamentals
A solid foundation in welding principles is crucial for achieving high-quality results.
Understanding different welding processes, including MIG (Metal Inert Gas), TIG (Tungsten Inert Gas), and Stick welding, is crucial, as each method has its applications, benefits, and limitations. Knowing when to use each technique ensures that you choose the most efficient and appropriate method for your projects.
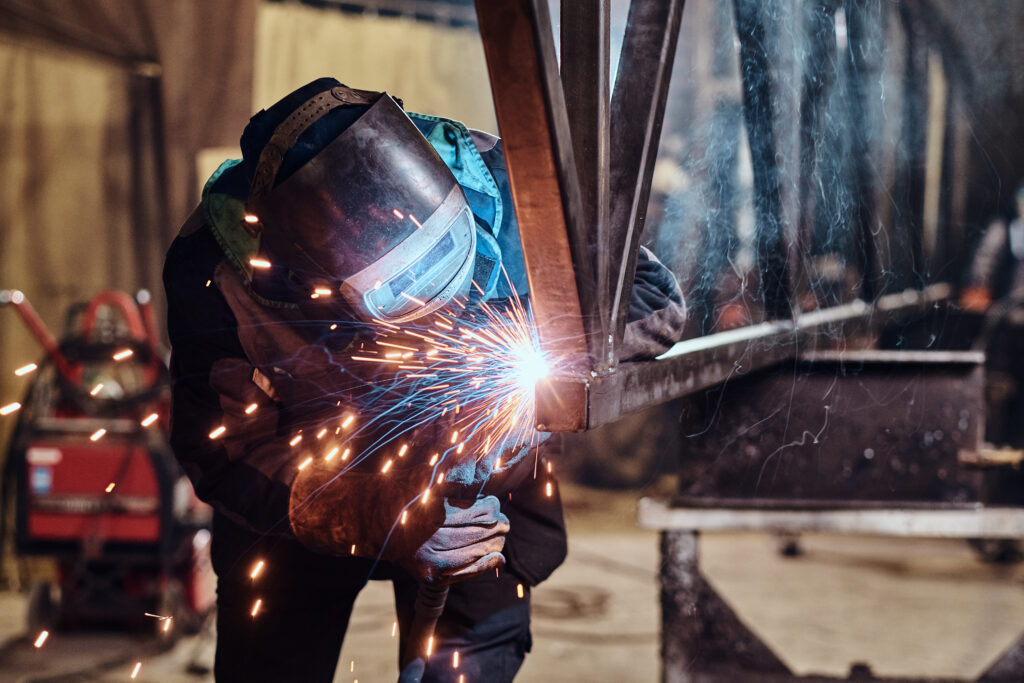
Moreover, it is important to familiarize yourself with the materials you are working with. Various metals have different properties, such as melting points and conductivity, which affect how they respond to heat and filler materials. Welding steel, aluminum, or stainless steel requires specific approaches, and selecting the right shielding gas and filler metal is essential for strong, durable welds.
Additionally, understanding fundamental welding techniques like maintaining proper travel speed, work angle, and arc length can significantly impact the quality of your work. Consistently practicing these techniques will lead to smoother, stronger, and more precise welds.
2. Seek continuous learning and certification
Welding is a profession that requires ongoing learning and adaptation. Industry standards, materials, and techniques continuously evolve, so keeping yourself updated with the latest advancements is essential for career growth and skill development.
Enrolling in advanced training programs, attending workshops, and participating in industry conferences help you stay ahead of emerging trends. Many institutions offer specialized welding courses that focus on areas such as pipeline welding, aerospace welding, and underwater welding, allowing you to expand your expertise and explore new career paths.
Certification is another key aspect of professional development. Obtaining certifications from recognized institutions not only validates your skills but also enhances your credibility and employment opportunities. Certified welders often have access to better job opportunities, higher salaries, and greater career stability.
Additionally, networking with experienced welders and joining professional welding communities can provide valuable insights, mentorship, and opportunities for collaboration.
3. Prioritize safety and equipment maintenance
Safety should always be the top priority when welding. Welding involves exposure to extreme heat, sparks, and hazardous fumes, so wearing the appropriate personal protective equipment (PPE) is essential. Always wear appropriate, including welding helmets, gloves, and flame-resistant clothing.
Beyond personal safety, maintaining your equipment is just as critical. Regular inspections and upkeep of welding machines, cables, torches, and consumables ensure optimal performance and prevent defects that could compromise weld quality.
A well-maintained welding machine also contributes to efficiency and consistency, reducing downtime and increasing productivity. Keeping your workspace organized and free from flammable materials minimizes hazards and creates a safer working environment.
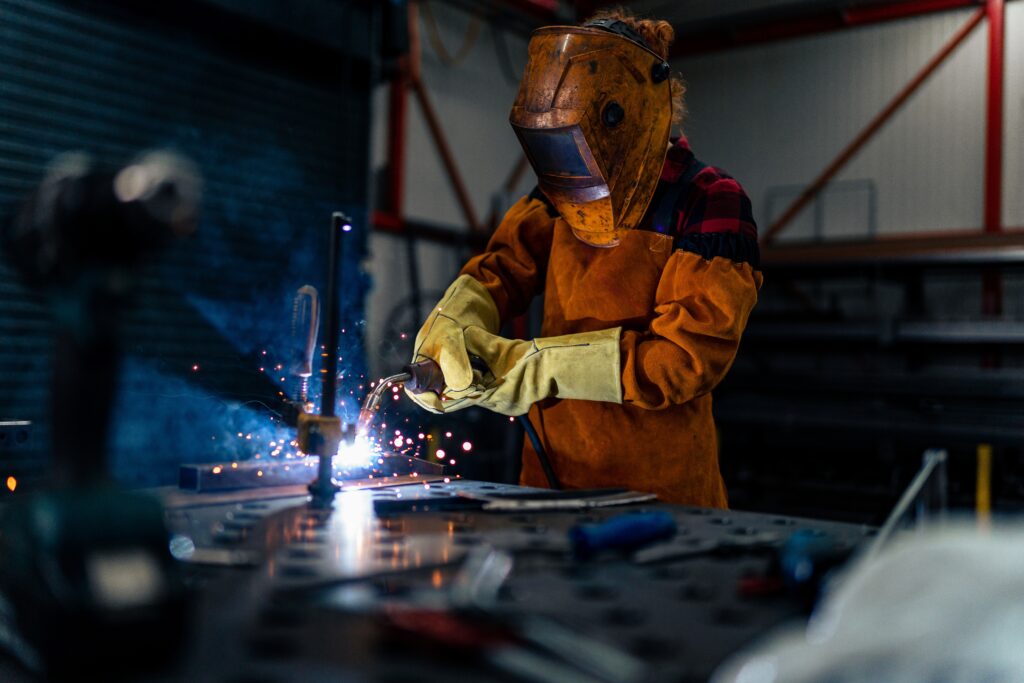
4. Embrace automation and digitalization
Staying up to date with the latest advancements in welding technology ensures that you remain competitive in an evolving industry. The welding industry is increasingly adopting automation and digital technologies. Automated welding systems and digital monitoring tools are transforming how welding is performed, making processes more precise, repeatable, and efficient.
Robotic welding systems are increasingly being used in industrial settings for mass production, reducing human error and increasing output. While traditional welding still requires skilled professionals, understanding and adapting to automated welding systems can make you a more valuable asset in the industry.
Digital tools, such as welding data management software, allow welders to monitor parameters in real-time, analyze weld quality, and optimize performance. These innovations improve consistency in welds and help identify areas that need improvement.
Familiarize yourself with automated welding systems and digital tools that can assist in monitoring and controlling welding parameters. Understanding how to operate and troubleshoot these systems can make you a more versatile and valuable welder in the modern industrial landscape.
5. Leverage Augmented Reality (AR) welding simulators
With advancements in technology, AR welding simulators have become a game-changer in training and skill development. These cutting-edge tools provide a risk-free, cost-effective, and highly immersive learning environment, allowing welders to practice their techniques without the need for actual materials or hazardous conditions. Incorporating AR welding simulators into your training regimen can significantly enhance your skills.
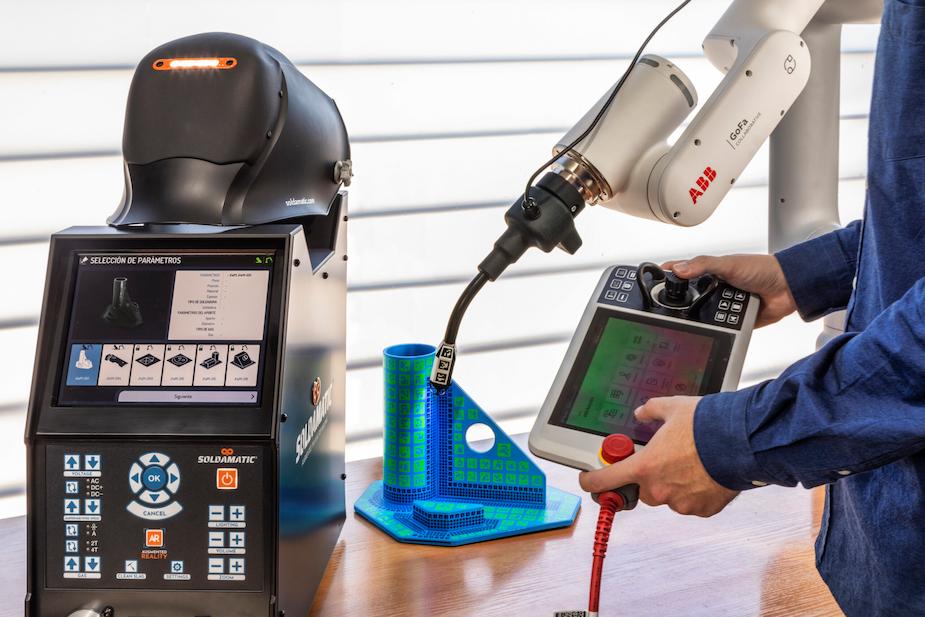
Soldamatic utilizes HyperReal-SIM™ technology to create lifelike welding practices. This system offers real-time feedback on parameters such as travel speed, electrode angle, and heat input, enabling users to refine their techniques efficiently. This welding simulator also promote sustainable training by reducing the consumption of consumables like electrodes and shielding gas, making them an environmentally friendly alternative to traditional training methods.
Integrating Soldamatic into training programs accelerates the learning curve, enhances retention of knowledge, and provides a consistent, repeatable learning experience. This is especially beneficial for industrial training centers and vocational schools looking to prepare the next generation of skilled welders.
Advancing your welding skills
Improving your welding technique requires dedication, practice, and a willingness to embrace new technologies. By mastering the fundamentals, prioritizing safety, adopting automation, and continuously learning, you can refine your skills and achieve higher-quality welds.
With the rise of digitalization and automation, modern welding solutions such as augmented reality welding simulators have revolutionized the learning process, making it easier to hone skills effectively. Investing time in skill development not only enhances your craftsmanship but also opens doors to new opportunities in the industrial and manufacturing sectors. Stay committed to improving your technique, and the results will reflect in the quality of your work.
By implementing these tips, you can significantly improve your welding technique, leading to higher quality work and greater career satisfaction. Remember, consistent practice, staying informed about industry developments, and embracing innovative technologies like Soldamatic are key components to becoming a proficient welder.