Flux-Cored Arc Welding (FCAW) is a versatile and efficient welding technique widely used in various industrial applications. This article delves into the intricacies of the FCAW process, its advantages and limitations.
Understanding FCAW
FCAW is a semi-automatic or automatic arc welding process that utilizes a continuous, consumable tubular electrode filled with flux. The heat generated by an electric arc between the electrode and the workpiece melts both the base metal and the electrode, forming a weld joint. Depending on the specific requirements, FCAW can be performed with or without an external shielding gas.
Types of FCAW
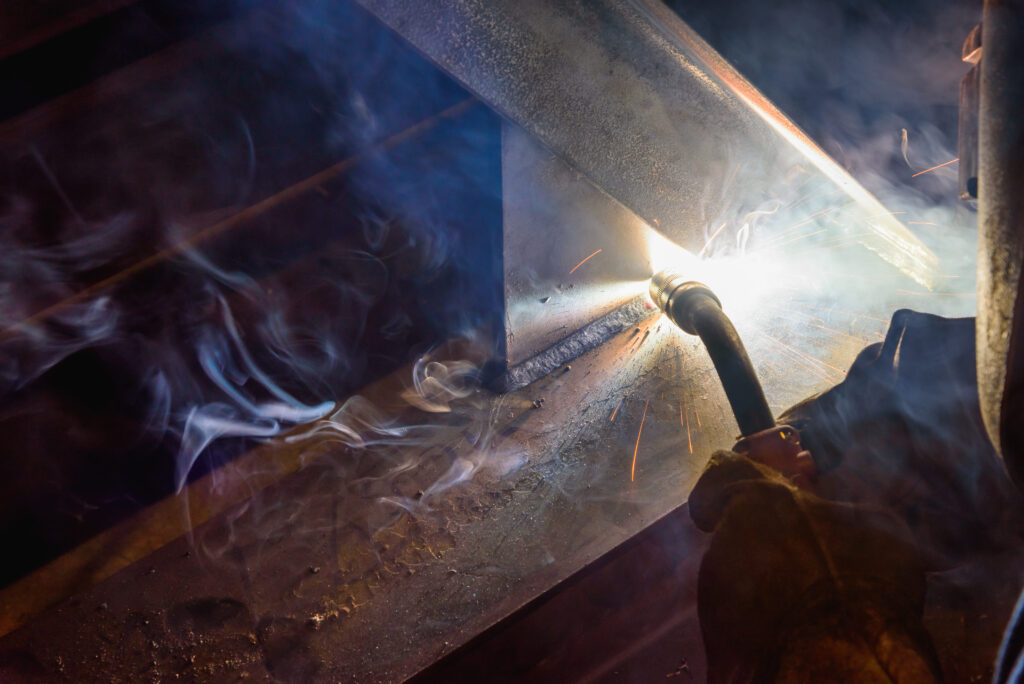
1. Self-Shielded FCAW (FCAW-S): This method relies solely on the flux core within the electrode to produce shielding gases that protect the weld pool from atmospheric contamination. It is particularly advantageous for outdoor applications due to its portability and resistance to windy conditions.
2. Gas-Shielded FCAW (FCAW-G): Also known as “dual shield” welding, this technique employs an external shielding gas, such as carbon dioxide or a mixture of argon and carbon dioxide, in addition to the flux core. This combination enhances weld quality and is preferred for welding thicker materials or out-of-position welding.
Advantages of FCAW
- High deposition rates: FCAW offers higher deposition rates compared to other welding processes, leading to increased productivity.
- All-position welding: With the appropriate filler materials, FCAW can be performed in all positions, providing flexibility in various welding scenarios.
- Reduced pre-cleaning: The process is more forgiving of surface contaminants, reducing the need for extensive pre-cleaning of the base metal.
- Outdoor suitability: Self-shielded FCAW is well-suited for outdoor environments, as it does not require external shielding gas, making it less susceptible to wind interference.
Strengths of FCAW
- High productivity: The process allows for faster welding speeds and thicker weld deposits, which can boost efficiency in industrial settings.
- All-weather use: Self-shielded FCAW is particularly useful in outdoor or fieldwork scenarios, as it doesn’t rely on external shielding gas.
- Flexibility: The ability to weld in all positions (flat, vertical, horizontal, and overhead) makes it versatile across industries like construction, shipbuilding, and heavy machinery.
Challenges and limitations of FCAW
- Fume generation: FCAW tends to produce more smoke and fumes than other welding processes, necessitating proper ventilation and safety measures.
- Slag removal: The formation of slag requires additional time for removal between weld passes, which can affect overall efficiency.
- Higher consumable costs: The specialized tubular electrodes used in FCAW can be more expensive than solid wires used in other processes.
Flux-Cored Arc Welding (FCAW) process |
||
Advantages |
Strengths |
Challenges |
High deposition rates | High productivity | Fume generation |
All-position welding | All-weather use | Slag removal |
Reduced pre-cleaning | Flexibility | Higher consumable costs |
Outdoor suitability |
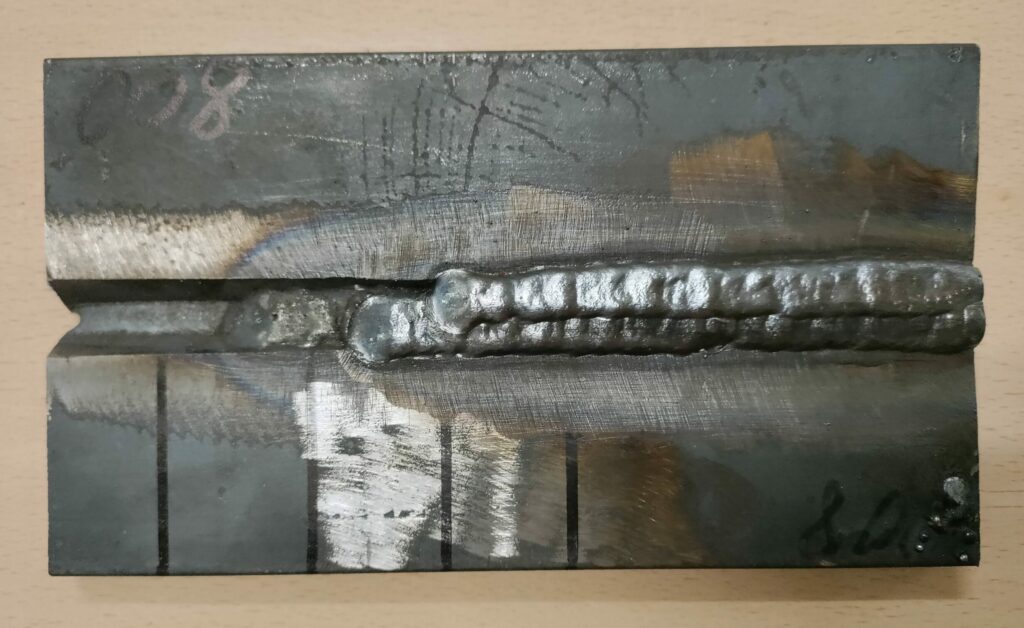
Augmented Reality in welding training
The integration of Augmented Reality (AR) into welding training has revolutionized the way welders acquire their skills. AR-based welding simulators, such as Soldamatic, provide immersive and interactive training environments that replicate real-world welding scenarios.
Soldamatic is a pioneering AR welding simulator that combines cutting-edge technology with comprehensive training modules. It offers a range of features designed to enhance the learning experience:
· Realistic Simulation: Utilizing HyperReal-Sim™ technology, Soldamatic delivers highly accurate welding practices.
· Comprehensive Curriculum: The simulator includes a wide array of welding processes and positions, catering to various skill levels and training requirements.
Soldamatic’s Advanced Welding Multijoints to practice FCAW |
|
AWM001 | Foundational Ambidex |
AWM002 | Foundational Complex Sequence |
AWM003 | Heavy Industry Specific Practices |
AWM004 | Automotive Chassis Assembly |
AWM005 | Automotive Thin Plates |
AWM006 | Shipbuilding Open Root |
AWM008 |
Pipeline 6” Schedule 80 |
The integration of digital tools, such as Augmented Reality (AR), enhances training for FCAW in a more accessible and sustainable path. Soldamatic enable trainees to practice FCAW in a virtual environment, offering cost savings and reducing waste while maintaining safety.
FCAW welding: a key to industrial excellence
Flux-Cored Arc Welding (FCAW) stands as a robust, efficient, and adaptable welding process, suitable for a multitude of industrial applications. Its key benefits include high deposition rates, adaptability to different positions, and suitability for outdoor use, especially in challenging environments where wind or contamination might pose issues for other processes.
Soldamatic represents an important milestone in the digitization and automation of welding instruction. By embracing these technological advancements, the industry can cultivate a skilled workforce equipped to meet the evolving demands of modern manufacturing.