Welding symbols play a crucial role in the world of fabrication and engineering. They are used in technical drawings to convey detailed information about welding operations. These symbols ensure that welds are performed accurately and consistently, adhering to design specifications and quality standards. Read the article to know the key reasons why welding symbols are vital in the industry.
What is a Welding Symbol?
A welding symbol is a standardized graphical representation used in technical drawings to communicate specific details about welding operations required to create a part or assembly. These symbols are a part of the engineering and drafting language used to convey precise information about how a weld should be performed, including its type, size, location, and other pertinent details.
Components, examples and meanings of Welding Symbols
Reference Line: The foundation of the welding symbol, the reference line is a horizontal line that serves as the baseline for all other elements. Instructions for the weld are placed above and below this line.
Arrow: A line that connects the reference line to the joint where the weld is to be made. The arrow can point up, down, left, or right, indicating the side of the joint where the weld should be applied.
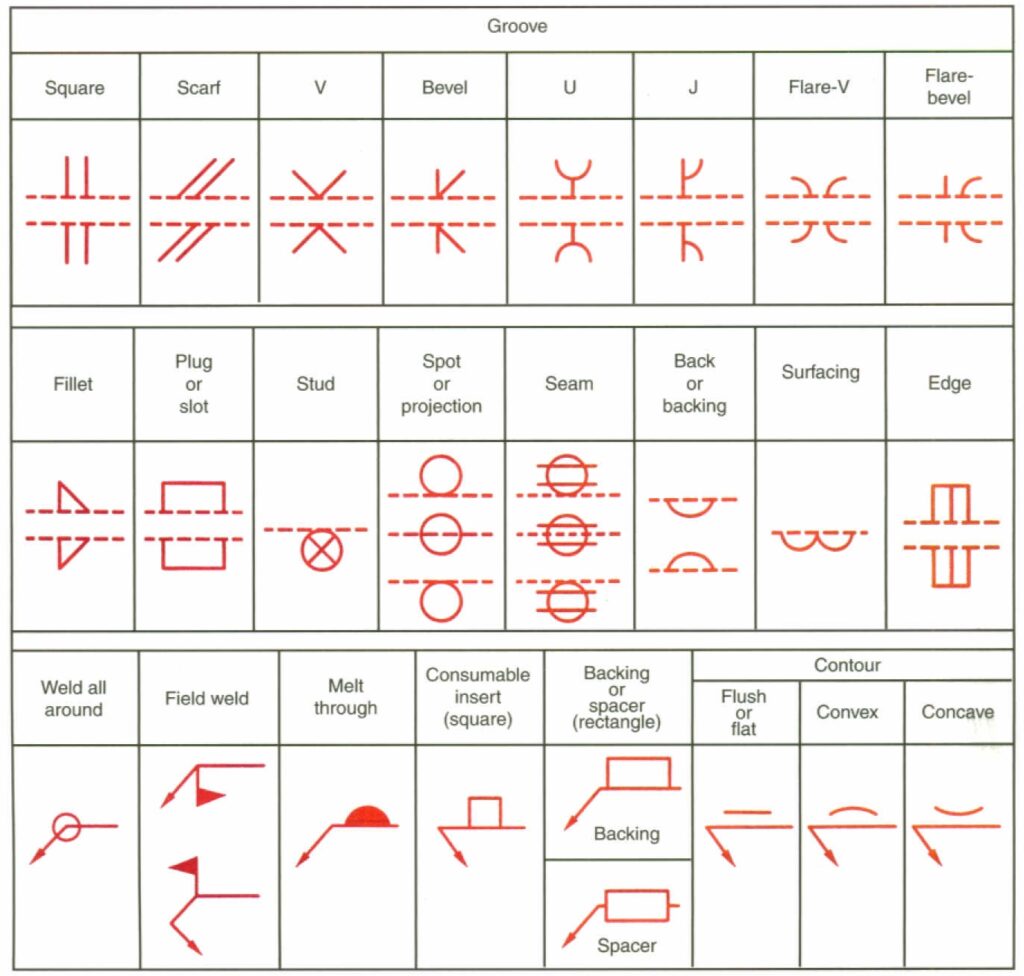
Basic Weld Symbol: Specific symbols placed on or near the reference line to indicate the type of weld required. Common weld symbols include:
- Fillet Weld (△): Represented by a triangle. Indicates a fillet weld, typically used for joining two surfaces at a right angle.
- Groove Weld: Various shapes depending on the groove type.
- (□) Used for a square groove weld, where the edges of the joint are prepared with a square cut.
- (V) Represents a V-groove weld, with edges beveled to form a V shape.
- (┌) Indicates a bevel groove weld, where one edge is prepared with a bevel.
- Plug or Slot Weld: Depicted by a rectangle.
- Spot or Projection Weld: Shown as a circle.
Dimensions and angles: Numbers and dimensions added to the welding symbol provide details on the size of the weld, such as leg length, throat thickness, and groove angle.
- Weld Size: Specifies the dimensions of the weld, such as leg size for fillet welds or depth for groove welds.
- Weld Length and Pitch: Specifies the length of the weld and the distance between intermittent welds.
Supplementary Symbols: Additional symbols to provide more specific information, such as contour, finish, or field weld symbols.
Reading Welding Symbols
Interpreting welding symbols correctly is crucial for fabricators and welders to execute the required welds accurately. Here you can find a step-by-step guide to read welding symbols:
1) Identify the Reference Line and Arrow: Determine the location and side of the joint where the weld is to be applied by following the arrow and reference line.
2) Examine the Weld Symbol: Look at the symbol on or near the reference line to identify the type of weld needed.
3) Check the Dimensions: Note any numbers or dimensions that provide additional details about the weld size and shape.
4) Review the Tail: If present, read the information in the tail for supplementary instructions or specifications.
How Welding Symbols can simplify complex processes?
These symbols are governed by standards such as AWS A2.4 in the United States and ISO 2553 internationally. They provide a clear and concise method for specifying weld types, sizes, lengths, and other essential parameters without cluttering the drawing with lengthy descriptions.
By providing clear and precise instructions, welding symbols facilitate efficient communication among engineers, designers, and welders, minimizing the risk of errors, enhancing safety, and ensuring the structural integrity of the final product.
- Standardization: By using standardized symbols, welding symbols ensure that all stakeholders, regardless of their location or language, understand the welding requirements in the same way.
- Clarity and Precision: Welding symbols provide a clear and precise way to convey all necessary information about the welding process, reducing misunderstandings and errors in fabrication.
- Efficiency: Detailed welding symbols can save time during the fabrication process as welders and fabricators do not need to seek additional clarifications or instructions.
- Quality Control: Accurate welding symbols help maintain consistent quality by ensuring that welds are performed according to the specified requirements and standards.
- Cost Savings: Properly specified welding symbols can prevent costly rework or repairs by ensuring the welds are correctly performed the first time.
- Safety: By ensuring that welds meet design specifications and standards, welding symbols contribute to the structural integrity and safety of the final product.
Enhancing welding precision: The AR Advantage
Soldamatic utilizes Augmented Reality (AR) to provide an immersive, interactive training environment where welders can practice and perfect their skills without the risks and costs associated with traditional welding training. By simulating real-world welding scenarios, Soldamatic allows trainees to visualize welding symbols and execute welds in a controlled, virtual setting. This hands-on approach accelerates the learning process, enabling welders to interpret welding symbols accurately and apply the correct techniques effectively. Moreover, AR technology like Soldamatic offers instant feedback and detailed performance analytics, helping trainees identify and correct mistakes in real-time. This iterative learning process fosters a deeper understanding of welding concepts and enhances the precision and quality of the welds.
Incorporating AR training solutions such as Soldamatic into welding education bridges the gap between theoretical knowledge and practical application. By leveraging AR, welders can master the interpretation and execution of welding symbols with greater efficiency and confidence, ultimately contributing to higher standards of craftsmanship and safety in the welding industry.
As technology continues to advance, tools like Soldamatic will play an integral role in shaping the future of welding training, ensuring that the next generation of welders is equipped with the skills and expertise needed to meet the demands of the industry.
Bridging knowledge of welding symbols and practice with Soldamatic
By mastering the interpretation of welding symbols, you can ensure high-quality welds that meet design specifications and industry standards. Taking the time to learn and understand welding symbols will undoubtedly enhance your skills and contribute to the success of your projects, because understanding welding symbols is essential for anyone involved in welding and fabrication.
In today’s fastly evolving technological landscape, mastering welding techniques requires more than just understanding welding symbols and practical experience. Augmented Reality has emerged as a transformative tool in this regard, offering unprecedented opportunities for training and skill enhancement, and Soldamatic is one exemplary application of AR in welding.