Welding robots have revolutionized the manufacturing industry, bringing efficiency, precision, and speed to the welding process. These robotic systems are designed to handle various welding tasks, making them indispensable in modern production lines. In this article you will delve into the diverse types of welding robots, each tailored to specific applications, and explore their key features and advantages.
Types of Welding Robots: History, Purpose and Definition
Robot welding was introduced in the industrial sector during the 1960’s. This method is extensively used in manufacturing industries for applications ranging from automotive assembly to aerospace fabrication.
Welding robots are automated systems designed to perform welding tasks with precision, speed, and efficiency. These robots are equipped with robotic arms that can manipulate welding tools to join materials together (typically metals) using various welding techniques (SMAW, TIG, GMAW…).
Articulated Welding Robots
Articulated robots are the most common type of welding robots and are characterized by their multi-jointed arms, resembling a human arm. These robots are versatile and can perform welding tasks in various orientations. Their flexibility makes them suitable for applications requiring a wide range of motion, such as welding complex geometries.
Advantages:
- High flexibility.
- Excellent range of motion.
- Versatility in welding applications.
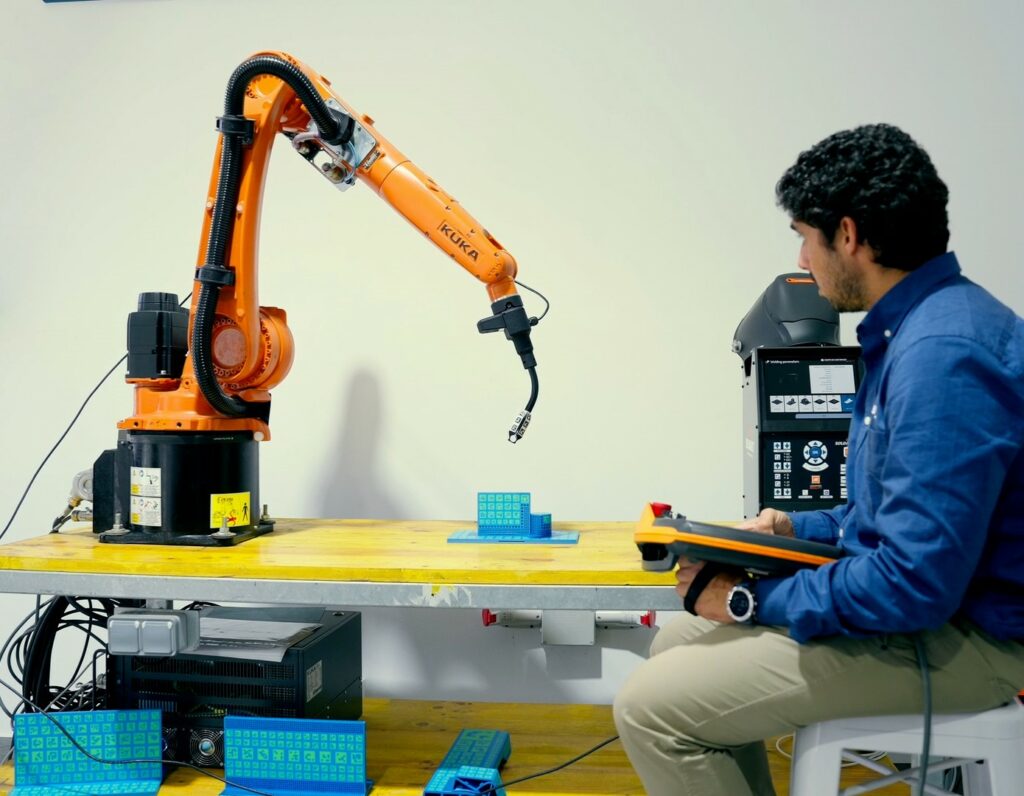
Resistance Spot Welding Robots
This type of robot is common in the automotive industry, focused on assembling vehicle body sections, as some of their materials are resistant to electrical currents and it makes unsuitable for other types of welding. The spot-welding robot overcomes the issue by joining two thin metal sheets in a unique area using a variety of resistance welding.
Advantages:
- Improved product quality.
- Increased welding speed and accuracy.
- Better workpiece access.
Collaborative Welding Robots (Cobots)
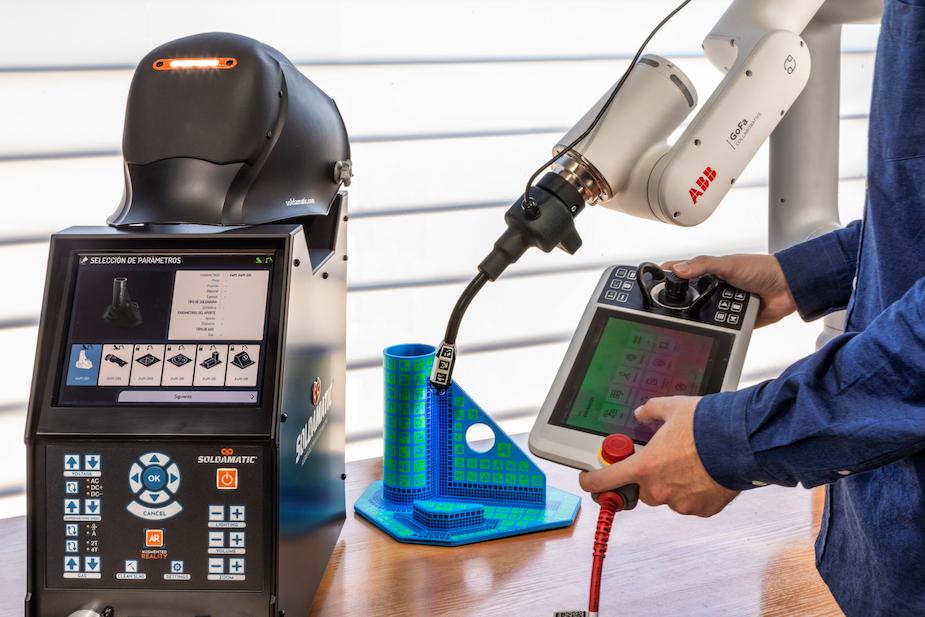
Collaborative robots are designed to work alongside human operators, enhancing efficiency and safety in the welding environment. These robots are equipped with sensors and safety features to detect and respond to human presence, allowing for seamless collaboration.
Advantages:
- Safe collaboration with human operators.
- Increased efficiency.
- Adaptable to changing tasks.
Types of Welding Robots: Comparative Analysis
Articulated Welding Robots | Resistance Spot Welding Robots | Collaborative Welding Robots |
High Flexibility | Improved product quality | Safe collaboration with human operators |
Excellent range of motion | Increased welding speed and accuracy | Increased efficiency |
Versatility in welding applications | Better workpiece access | Adaptable to changing tasks |
Augmented Reality applied to the different Types of Robots
As technology continues to advance, welding robots play an increasingly significant role in the manufacturing landscape. However, the sector’s progress is constrained by the global shortage of qualified operators. Augmented Reality (AR) offers a transformative approach to training operators for robot welding, presenting several advantages that enhance efficiency and proficiency in the learning process.
Realistic Simulation and Customized Learning Paths
Augmented Reality provides a realistic and immersive training environment where operators can simulate robot welding scenarios.
AR technology facilitates the usage of a real robot’s teach pendant while providing training opportunities for operators for specific welding routines. AR platforms enable the creation of customized training modules based on specific practices and requirements. Operators can focus on improving their skills in areas that align with their job responsibilities, ensuring targeted and efficient learning tailored to the needs of the industry or organization.
Enhanced Safety and Reduced Resource Consumption
Robot welding often involves inherent risks, especially for novice operators. Augmented Reality allows trainees to practice in a risk-free virtual space, and eliminates the need for such physical resources by enabling training through simulations, leading to practice in a safe environment and significant cost savings for both equipment and materials. Traditional training methods often require the use of actual robots and materials, consuming resources and increasing costs.
Accessibility and Immediate Feedback
AR training can be accessed remotely, providing flexibility for operators to learn at their own pace and convenience. This is particularly advantageous for organizations with geographically dispersed teams, allowing consistent and standardized training regardless of location.
You can simultaneously evaluate your trainees. This technology provides instant feedback to operators, allowing them to assess their performance in real-time. Immediate feedback accelerated the learning curve, as operators can identify and correct mistakes quickly, leading to a faster and more effective skill acquisition process.
Soldamatic Robotics is connected to a Robot Arm
The field of robotics and welding is dynamic, with continuous technological advancements. Augmented Reality training platforms can easily integrate updates and new features, ensuring that operators stay current with the latest developments in robot welding technology.
Soldamatic technology seamlessly integrates with any robot available in the market, offering an extensive catalog of dedicated joints for robotic welding along with specific training content: there are welding joints for different levels to improve your operator’s skills and flexible content adaptable to your center.
Soldamatic Robotics modernizes the welding training in the latest industry requirements. Many centers are applying this state-of-the-art technology. This solution uses real components while reducing risks and material consumption.
As a summary, Soldamatic Robotics is the most realistic, complete, flexible, and programmable robotic welding training.
Key considerations in welding automation: a welding robot, a purpose
The welding sector is progressively embracing automation to enhance the quality of welding and adhere to increasingly stringent standards.
The diverse types of welding robots cater to different applications, offering solutions that range from precision-based tasks to high-speed operations, and Soldamatic can be integrated in any robot in the actual market. Understanding the characteristics and advantages of each type of welding robot is crucial for manufacturers seeking to optimize their welding processes and stay ahead in the competitive world of modern industry.