Plasma arc welding (PAW) is an advanced welding technique that builds upon the principles of gas tungsten arc welding (GTAW), commonly known as TIG welding. Both processes utilize a non-consumable tungsten electrode to generate the electric arc necessary for welding.
How Plasma Arc Welding works
PAW distinguishes itself by constricting the arc through a fine-bore copper nozzle, resulting in a highly concentrated plasma jet capable of reaching temperatures up to 28,000°C (50,000°F).
In PAW, the tungsten electrode is positioned within the torch body, separating it from the shielding gas envelope. An electric arc forms between the electrode and the workpiece, ionizing the plasma gas, which is typically argon or a mixture of argon and hydrogen.
Advantages of PAW |
|
Precision |
The constricted arc allows for accurate control, making it ideal for intricate welds. |
High penetration |
Capable of welding thick materials in a single pass, enhancing efficiency. |
Stability |
Offers a stable arc, reducing defects and improving weld quality. |
This ionized gas is then expelled through the constricting nozzle, producing a high-velocity plasma jet that melts the base material, facilitating coalescence. The process may or may not involve the addition of filler metal, depending on the specific application.
Various types of Plasma Arc Welding
Plasma Arc Welding (PAW) has two main modes of operation: transferred arc and non-transferred arc. These modes affect how the arc interacts with the workpiece, influencing the welding process and its applications.
Key differences
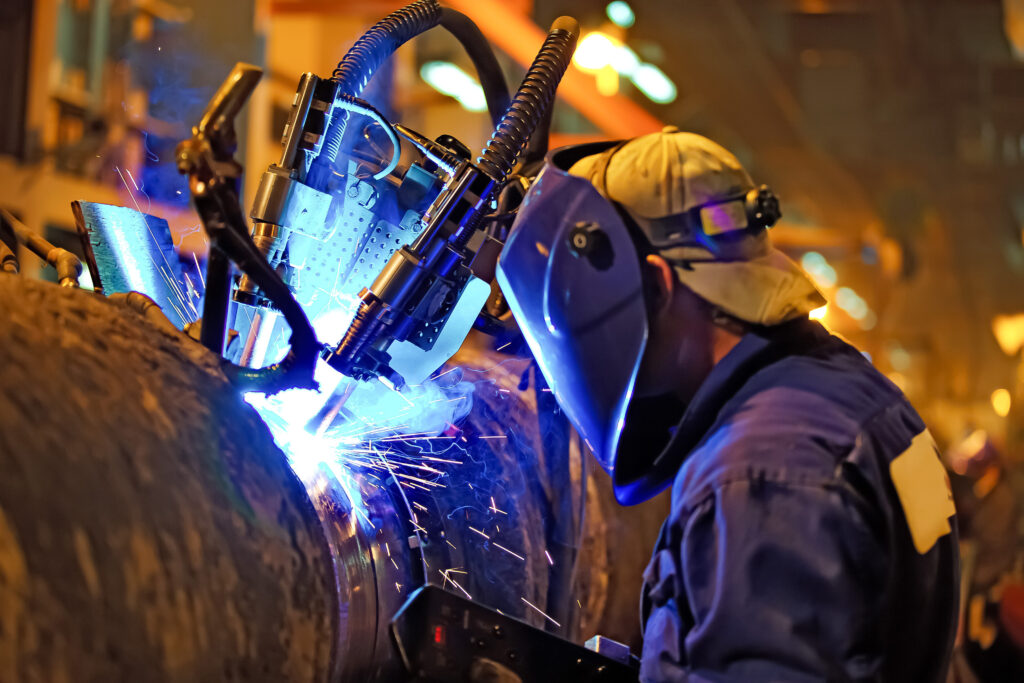
1) Energy focus: Transferred is more powerful and concentrated; non-transferred is more diffused.
2) Circuit path: Transferred includes the workpiece in the circuit; non-transferred keeps the arc within the torch.
3) Material thickness: Transferred handles thicker materials; non-transferred is better for thin or delicate materials.
Plasma Arc Welding comes in three main types, each suited to different applications depending on the material thickness and precision required.
These variations give PAW a lot of versatility, whether you need ultra-fine precision or heavy-duty power. This versatility makes PAW applicable across various industries, including aerospace, chemical processing, and petrochemical sectors.
Micro Plasma Arc Welding (Micro-PAW) |
Medium Current Plasma Arc Welding |
High Current Plasma Arc Welding |
|
Current range |
0.1 to 15 amps | 15 to 100 amps | 100 to 300+ amps |
Applications |
Welding very thin materials (as thin as 0.1 mm), like medical devices, jewelry, and aerospace components. | General-purpose welding of thin to moderately thick materials in industries like automotive and electronics. | Heavy-duty industrial welding, such as shipbuilding, pressure vessels, and thick structural components. |
Key feature |
Produces an ultra-fine, stable arc, making it perfect for precision work on delicate materials. | Balances precision and power, offering good penetration while still being relatively controlled. | Produces a highly concentrated plasma jet capable of deep penetration and high deposition rates, making it ideal for thicker materials. |
Despite its unique features, PAW shares commonalities with other welding methods:
- Arc-based process: Like many welding techniques, PAW relies on an electric arc to generate the heat necessary for welding.
- Versatility: PAW can be applied to a wide range of metals, including stainless steel, aluminum, and titanium, similar to GTAW and GMAW.
- Shielding requirements: To protect the molten weld pool from atmospheric contamination, PAW employs shielding gases, a practice common in processes like GTAW and GMAW.
Differences between Plasma Arc Welding and other welding processes
Gas Tungsten Arc Welding (GTAW/TIG) | Gas Metal Arc Welding (GMAW/MIG) | Shielded Metal Arc Welding (SMAW/Stick) |
While both PAW and GTAW use a non-consumable tungsten electrode, PAW’s constricted arc results in a higher energy density.
This allows for deeper penetration and faster welding speeds compared to GTAW.
Additionally, PAW offers greater arc stability, enabling longer arc lengths and improved tolerance to variations in arc length. |
GMAW employs a consumable wire electrode and typically requires a continuous supply of shielding gas.
In contrast, PAW uses a non-consumable electrode and a plasma gas to create the arc, resulting in a more focused heat source.
This focus provides better control over the weld pool, making PAW suitable for applications requiring precision. |
SMAW utilizes a consumable electrode coated in flux, which produces a shielding gas when heated.
PAW’s use of a plasma gas and separate shielding gas allows for cleaner welds with less slag formation, reducing the need for post-weld cleaning. |
Advancements in welding
The integration of augmented reality (AR) into welding training has revolutionized the way welders acquire and improve their skills.
Seabery Welding Simulator is an AR-based welding solution that provides immersive training experiences by replicating real-world welding practices without the need for consumables or exposure to hazardous environments.
The simulator provides immediate feedback on technique, highlighting issues like incorrect torch angles, travel speed, or unstable arcs. This feedback helps learners quickly refine their skills, leading to better weld quality when they transition to live welding. It is a powerful tool for building confidence and competence before striking an actual arc.
Incorporating AR into welding aligns with the broader trends of automation and digitalization in the industrial sector. By embracing these technologies, training programs can produce highly skilled welders proficient in advanced techniques, meeting the evolving demands of modern manufacturing and construction industries.
Why Plasma Arc Welding stands out
Plasma arc welding stands out as a precise and efficient welding process, offering advantages over traditional methods through its concentrated heat source and deep penetration capabilities. Understanding the operation and benefits of PAW is crucial for industries requiring high-quality welds, as it provides a reliable and efficient solution for various welding challenges.
As the industry continues to evolve with automation and digitalization, integrating technologies like augmented reality into training programs ensures that the next generation of welders is well-equipped to master advanced welding techniques, including PAW.