Welding is a cornerstone of industries ranging from construction and manufacturing to shipbuilding and aerospace. However, traditional training methods for welders can be expensive, time-consuming, and resource-intensive. The introduction of innovative technologies is revolutionizing the way industries approach welder training. These solutions significantly reduce costs and increase efficiency, and we are going to talk about them in this article.
The challenges of traditional welding training
Conventional welding training programs often require a significant investment in consumables such as metal plates, wires, gases, and welding machines. Additionally, these programs generate a substantial amount of waste material, which can be both costly and environmentally damaging. Traditional methods also expose trainees to safety risks during their initial learning phases.
Another challenge is the limited availability of expert trainers and suitable training facilities, particularly in remote areas. Combined, these factors can hinder the scalability of welder training programs and increase operational costs for industrial organizations.
Augmented Reality: a game-changer in welding education
Augmented Reality (AR) has emerged as a powerful tool to bridge the gaps in traditional training methods. An AR-based welding simulator provides an immersive, realistic training environment where learners can practice their skills without consuming actual resources. The technology replicates real-world welding scenarios, enabling trainees to interact with virtual workpieces and tools while receiving real-time feedback.
Benefits of AR welding simulators |
1) Improved safety |
2) Enhanced learning efficiency |
3) Scalability |
4) Cost savings |
5) Environmental impact |
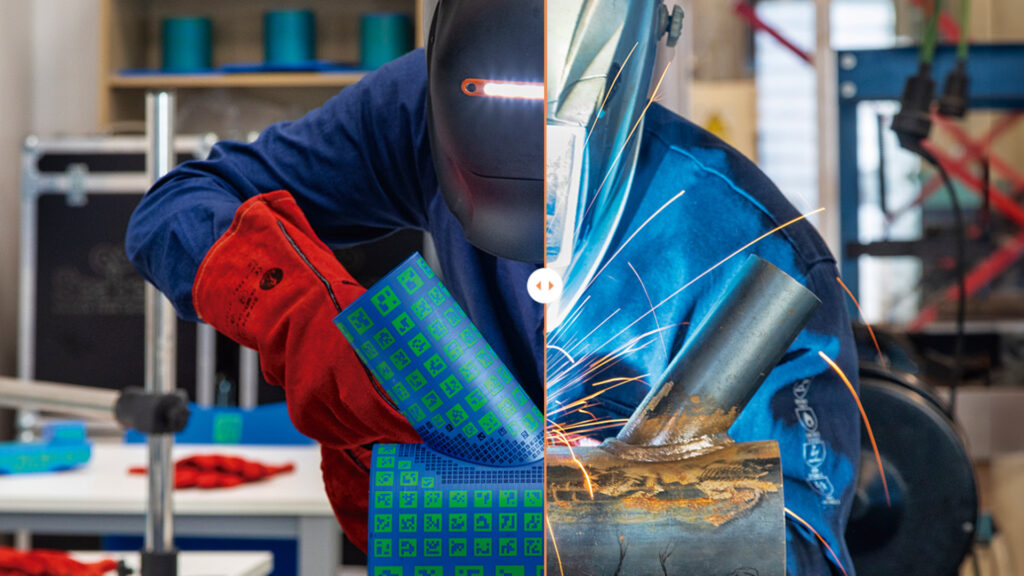
1) AR simulators create a risk-free environment for beginners, allowing them to practice techniques and correct mistakes without exposure to high temperatures, UV radiation, or other hazards associated with live welding.
2) There are welding simulators that provide real-time analytics and performance tracking, enabling personalized feedback for trainees. This accelerates the learning curve and ensures that students achieve competency faster.
3) With AR simulators, training can be conducted anywhere, without the need for extensive infrastructure. This scalability makes it easier for companies to train large numbers of welders across multiple locations.
4) By eliminating the need for consumables like metal and gas, AR welding simulators significantly reduce material costs. Trainees can repeat tasks as often as necessary without additional expenses, making the training process more economical in the long run.
5) The reduced reliance on consumables means less waste and a smaller environmental footprint. For industries committed to sustainability, integrating AR solutions into training programs aligns with green initiatives.
Real-world applications of AR welding simulators
Industrial services companies are leveraging AR welding simulators to address skill gaps and ensure high-quality welding output. Incorporating AR simulators into training programs also allows companies to meet certification standards more efficiently. Trainees can practice and refine their skills in simulated environments before transitioning to live welding, reducing the time required to achieve certification.
Soldamatic is used globally in vocational training centers, technical schools, and corporate training programs. Its effectiveness in training both novices and experienced welders has made it a preferred solution for organizations aiming to upskill their workforce.
Why Soldamatic stands out
Soldamatic is a leader in the AR welding simulation space, offering a comprehensive solution tailored to industrial needs. Its cutting-edge technology includes:
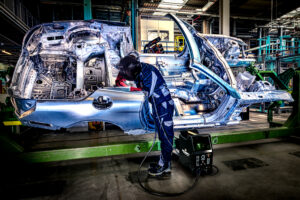
Customizable modules: Soldamatic allows trainers to adapt simulations to specific tasks or industries, enhancing relevance and effectiveness.
Realistic simulation: High-fidelity visuals and accurate tool mechanics replicate real-world welding scenarios. This technology is made for welders, by welders.
Global reach: Used in over 80 countries, Soldamatic has proven its versatility and scalability across diverse industrial sectors.
The future of industrial welding training
As industries adopt more advanced technologies, AR welding simulators will play a pivotal role in shaping the future of workforce development. They not only reduce costs and increase efficiency but also contribute to safer, more sustainable practices.
For industrial organizations seeking a competitive edge, integrating solutions like Soldamatic into their training programs is no longer a luxury but a necessity. By combining innovation with practicality, AR-based welding training is setting a new standard in industrial services.
Soldamatic significantly reduce costs and increase efficiency. This welding solution is an indispensable tool for modern industrial services. Would you like to explore how Soldamatic can transform your training program?