In the evolving landscape of industrial welding, ensuring consistency, safety, and quality is paramount. Central to achieving these objectives is the Welding Procedure Specification (WPS), a foundational document that delineates the parameters and methods for executing welds.
What is a Welding Procedure Specification (WPS)?
A WPS is a formal document that provides detailed guidelines to welders and welding operators for producing welds that meet specific code requirements. It encompasses essential variables such as base materials, welding processes, filler materials, joint design, preheat and post-weld heat treatment, welding positions, shielding gases, and electrical characteristics.
The primary goal of a WPS is to ensure that welds are performed consistently and safely across various projects and operators.
Key elements of a WPS |
Base material types |
Welding process (SMAW, GTAW, GMAW) |
Type of filler metal |
Joint design and geometry |
Preheat and interpass temperature |
Welding position (flat, horizontal, vertical, overhead) |
Electrical parameters (voltage, current, travel speed) |
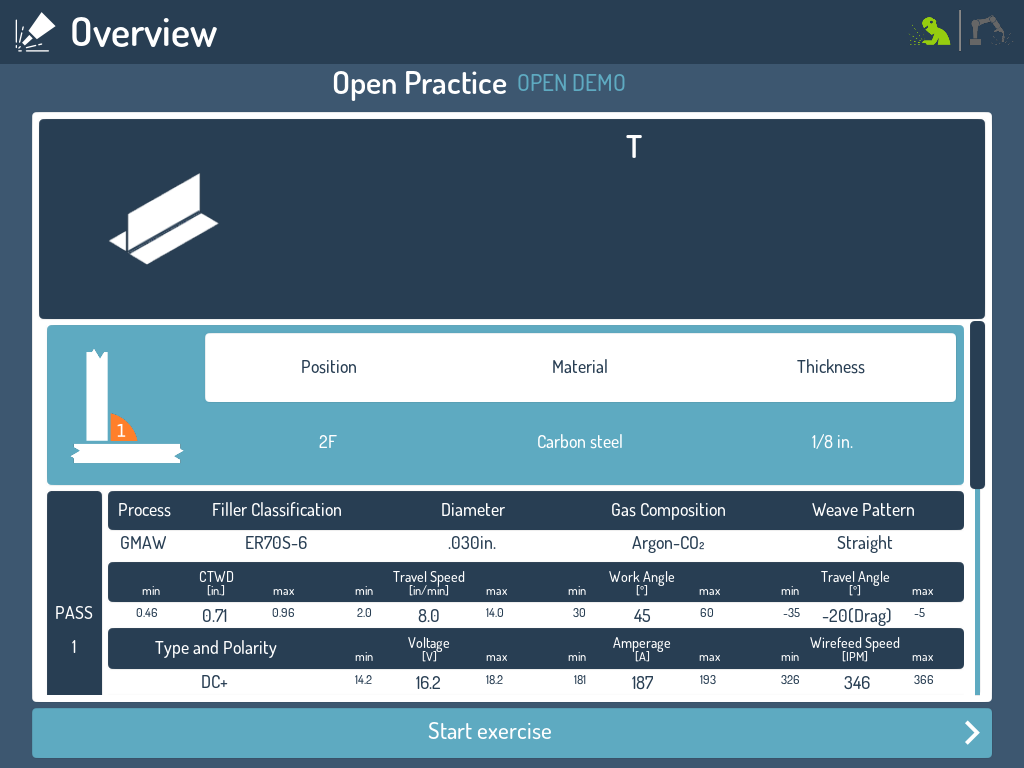
Types of WPS
WPSs can be categorized based on their development and application:
Prequalified WPS: Developed based on established welding codes and standards without the need for additional testing. These are typically used for routine welding tasks where proven procedures exist (Example: AWS D1.1).
Qualified WPS: Requires testing and validation through Procedure Qualification Records (PQRs) to ensure the welding procedure meets the necessary quality standards. This involves creating test welds and subjecting them to rigorous inspections.
Standard WPS: Generic procedures developed by industry organizations that can be adapted for multiple projects or industries. They serve as references for developing project-specific WPSs.
Common WPS Examples in Industrial Welding
The National Certified Pipe Welding Bureau (NCPWB) provides a comprehensive list of WPS examples tailored for various materials and welding processes. Here are some notable examples that illustrate the diversity of WPSs.
Description |
Applications |
|
WPS 1-1-1 | Shielded Metal Arc Welding (SMAW) using E6010 electrode with uphill progression without post-weld heat treatment (PWHT). | This is often used in structural welding and pipeline construction. |
WPS 1-3-1 | Gas Tungsten Arc Welding (GTAW) using ER70S-2 filler metal without PWHT. | Precise welds on thinner materials requiring higher weld quality. |
WPS 1-5-1 | Gas Metal Arc Welding (GMAW) Short Circuiting Transfer using ER70S-6 filler metal with CO₂ shielding gas without PWHT. | Used for light structural components and automotive manufacturing. |
WPS 4-2-1 | SMAW using E8018-B2 electrode with PWHT, suitable for Cr-Mo steels. | Used in high-temperature service conditions like boiler tubes or pressure vessels. |
WPS 8-3-1 | GTAW of thin-wall pipe without consumable insert. | Common in sanitary or high-purity piping systems. |
Importance of WPS in industrial applications
Implementing WPSs in industrial settings offers numerous benefits:
- Quality assurance: Ensures that welds meet specified standards, reducing the likelihood of defects.
- Safety compliance: Adherence to WPSs ensures compliance with safety regulations, protecting both workers and end-users.
- Efficiency: Standardized procedures streamline welding operations, reducing downtime and rework.
- Training and skill development: Provides a framework for training programs, ensuring that welders are equipped with the necessary skills and knowledge.
Integration of technology in WPS development and training
The advent of digitalization and automation has transformed the way WPSs are developed, validated, and taught:
Digital Documentation: Modern software solutions allow for the creation, storage, and retrieval of WPSs in digital formats, facilitating easy updates and distribution across teams.
Automated Welding Systems: Integration of WPS parameters into automated welding machines ensures consistent application of procedures, reducing human error and enhancing productivity.
Augmented Reality (AR) Welding Simulators: These tools provide immersive training environments where welders can practice procedures outlined in WPSs without the risks associated with live welding. This technology enhances understanding and retention of welding techniques.
How Digitalization enhance WPS Training and Execution
The adoption of digital tools has modernized how welding procedures are implemented, trained, and tracked. With the integration of technologies like Augmented Reality (AR) and automation, understanding and utilizing WPSs has become even more critical.
Seabery Welding Simulator offers realistic, hands-on training aligned with actual WPS parameters. These practices enable learners to practice welds virtually, reducing material costs, improving safety, and accelerating the learning curve.
A transformative solution
This welding simulator is built on cutting-edge Augmented Reality technology along with the integration of cameras that allows for continuous quality monitoring and feedback. Seabery’s technology analyzes the user performance against WPS standards, providing instant visual and quantitative feedback on arc length, angle, speed, and other critical metrics. Welders can train using custom or preloaded WPS configurations, ensuring that each exercise reflects real-world industrial requirements.
By reducing the need for physical consumables, the simulator allows unlimited practice without wasting materials, which is ideal for high-volume training environments. From base materials and joint configurations to travel speed and electrode angles, the simulator replicates the full range of welding parameters defined in WPS documents. With Seabery’s AR solution, industrial and educational welding robots can also be programmed with WPS-compliant parameters, ensuring consistent weld quality across high-volume production runs.
Seabery’s solution supports the digitalization goals of Industry 4.0 by combining automation, data analytics, and immersive learning. The simulator also enables instructors and supervisors to monitor skill progression remotely, verify WPS compliance, and adjust training programs dynamically.
Ensuring weld integrity with WPS
Welding Procedure Specifications (WPSs) are integral to the success of industrial welding operations. As industry embraces digitalization, automation, and technologies like Augmented Reality, the role of WPSs becomes even more critical in ensuring quality, safety, and efficiency.
As industries worldwide adopt smarter methodologies for workforce development, Seabery Welding Simulator provides a scalable, efficient, and forward-thinking approach to welding education—anchored in the same principles that define WPS: repeatability, reliability, and quality.
By understanding and effectively implementing WPSs, industries can achieve superior welding outcomes and stay ahead in a competitive landscape.