Collaborative robots or “cobots” have transformed modern manufacturing, offering unprecedented flexibility and efficiency in welding processes. This article explores the benefits of cobot welding and the future prospects of this innovative approach in modern manufacturing.
What is a Collaborative Robot?
A collaborative robot or “cobot”, is a type of robot designed to work alongside human operators in a shared workspace, enhancing productivity and efficiency without compromising safety. Cobot welding is particularly beneficial for small to medium-sized enterprises (SMEs) that may not have the resources for large-scale automation but still need to maintain high precision and quality in their welding processes.
Unlike traditional industrial robots that operate within isolated safety zones, cobots are designed to work alongside humans, enhancing productivity and safety. These robots are equipped with advanced sensors and safety features that allow them to detect human presence and adapt their actions accordingly. This enables them to perform tasks collaboratively with humans, leveraging the strengths of both. Cobots are highly versatile and can be easily programmed and reprogrammed for a variety of applications, making them particularly valuable in industries where flexibility and adaptability are crucial, including complex welding operations.
Understanding Cobot Weding
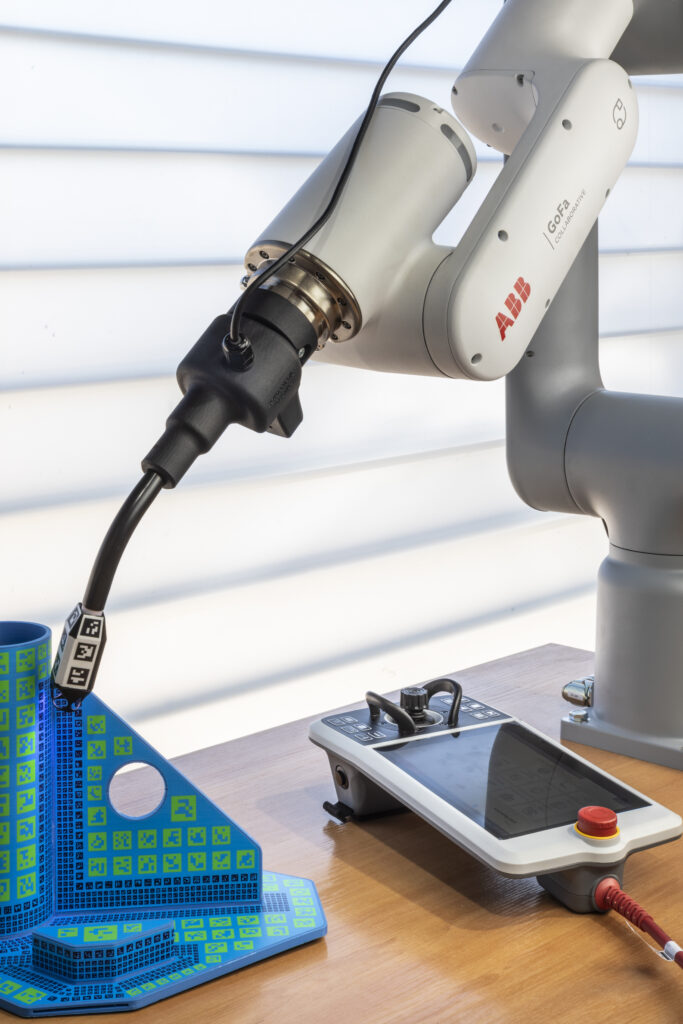
Advantage 1: Improved Quality and Consistency
Cobots excel at performing repetitive tasks with high precision, which is crucial in welding where consistency is key to product quality. By automating the welding process, cobots reduce the risk of human error and ensure uniformity in welds, resulting in products that meet stringent quality standards.
Advantage 2: Enhanced Flexibility and Adaptability
Cobots are designed to be easily reprogrammable, making them highly adaptable to changing production needs. This flexibility is especially valuable in industries where product lines frequently change or require customization. Unlike traditional robots that require extensive programming and setup, cobots can be quickly adjusted to perform new tasks, saving time and reducing downtime.
Advantage 3: Increased Safety and Collaboration
One of the primary advantages of cobots is their ability to work safely alongside human operators. Cobots can detect human presence and adjust their actions to prevent accidents. This collaborative environment not only enhances worker safety but also allows humans and robots to leverage their respective strengths—humans providing decision-making and problem-solving skills, and robots offering precision and endurance.
Advantage 4: Cost-Effectiveness
For SMEs, investing in cobot technology can be a cost-effective alternative to traditional automation solutions. Cobots are typically less expensive than their larger industrial counterparts and require less infrastructure and maintenance.
Several industries have successfully implemented cobot welding to enhance their manufacturing processes:
Applications for cobot welding across various industries |
|
Automotive |
Cobots are extensively used in the automotive industry for spot welding and assembling car body panels. They perform tasks with high precision and speed, ensuring consistency and quality in the manufacturing process.
Cobots can also handle tasks such as seam sealing and gluing, which are critical for maintaining vehicle integrity and safety. |
Aerospace |
Cobots are employed to perform intricate welding operations on aircraft components that require high accuracy and precision. They help in tasks like welding turbine blades and assembling fuselage sections, where human error can have significant consequences.
The use of cobots ensures uniformity and reduces the risk of defects in critical components. |
Cobots are ideal for metal fabrication tasks such as cutting, welding, and bending metal parts. They can handle a wide range of materials and thicknesses, making them versatile tools for custom fabrication jobs.
Cobots improve efficiency by performing repetitive tasks while allowing human operators to focus on more complex and creative work. |
|
Construction |
Cobots are increasingly being used in construction for welding steel structures, such as beams and columns, in prefabrication facilities. Their ability to work alongside humans makes them suitable for on-site applications where space and safety are concerns.
Cobots help improve the speed and accuracy of construction projects while reducing labor costs. |
Shipbuilding |
The shipbuilding industry utilizes cobots for welding large and complex metal structures, such as ship hulls and decks.
Cobots can handle the heavy lifting and precise welding required in this industry, reducing the physical strain on human workers and improving the overall efficiency of the shipbuilding process. |
Railway |
Cobots are utilized in the railway industry to weld components of train cars and tracks.
They help ensure the durability and safety of rail systems by providing high-quality welds and reducing human error. |
Soldamatic Robotics: The Future of Automation
One of the most significant advancements in cobot welding is the integration of augmented reality (AR) technology and simulation tools. AR allows operators to visualize welding paths, settings, and outcomes before actual welding occurs, providing a virtual overlay that enhances precision and reduces errors. The use of AR technology in the industrial sector has further optimized their manufacturing processes, allowing for real-time monitoring and adjustments to improve outcomes.
Soldamatic shows detailed guides onto workpieces, helping operators to better understand and execute welding tasks with the cobots. Simulation complements this by allowing manufacturers to model and optimize welding processes in a virtual environment, testing different scenarios without the risk of costly mistakes. By combining these technologies, manufacturers can achieve higher levels of efficiency, accuracy, and consistency in their welding operations.
The University of Kempten in Germany is one of the examples of how the Soldamatic Robotics technology is being implemented to train the industrial workers of the future. This university trains its students in manual welding with Soldamatic, and in the programming of robotic welding exercises with Soldamatic Robotics.
This allows students to use real robots, as well as the same equipment that is used in real robotic welding. This way, students are prepared to program real welding routines, just as they will do in their future jobs. If you want to know more about how the University of Kempten is applying Soldamatic, you can do so here.
Overcoming challenges in Cobot welding implementation
The integration of cobots with AR technology represents a significant step forward in manufacturing innovation. As these technologies continue to evolve, we can expect even greater improvements in the efficiency and effectiveness of welding processes. The potential for cobots to learn and adapt through machine learning could lead to even more sophisticated applications, opening up new possibilities for automation in industries worldwide.