Welding, the art and science of joining metals, plays a crucial role in a multitude of industries. Within this field, there are various specializations, each with its unique techniques, challenges, and applications. This article will show you the different industries which are related to the welding world.
Welding Industry Evolution: From Forge to Robotics
Until the end of the 19th century, forge welding was the only process used, until arc welding and oxy-fuel welding became dominant. The early 20th-century world war greatly contributed to the development of new cost-effective and reliable welding processes.
Rudimentary manual processes such as Shielded Metal Arc Welding (SMAW) emerged and remain popular today. From here, Gas Metal Arc Welding (MIG) and Flux Cored Arc Welding (FCAW) were developed. Advances in welding continued in the late 20th century with laser beam welding and robotic welding, both used in industrial environments.
You can also read more about the history of welding in our blog section.
Types of Welding Industries and Applications
Aerospace Industry
Aerospace welding demands the highest standards of precision and quality. Welds must endure extreme conditions, including high temperatures, pressure differentials, and vibrations.
- Fabricating aircraft frames and wings.
- Welding critical engine components.
- Joining fuel tanks and hydraulic systems
Railway Industry
Over a century ago, when steel rails were first introduced, welding became necessary to connect them together. In 1932, shot welding emerged as a pioneering method of spot welding, devised to efficiently fuse steel together.
Applications:
- Welding rails to create continuous tracks.
- Repairing and maintaining rail joints.
- Fabricating components for trains and locomotives.
Automotive Industry
In the automotive sector, welding is vital for manufacturing vehicles and their components. Precision and durability are vital, as the welds must handle extreme stresses and ensure the safety of the vehicle. Given that the average automobile requires thousands of welds, welding is likely to remain a fundamental aspect of the automotive industry unless significant changes occur.
Applications:
- Welding chassis and frame components.
- Joining body panels.
- Fabricating exhaust systems.
Manufacturing Industry
The manufacturing sector relies heavily on welding to produce machinery, equipment, and consumer goods. Welding covers a wide range of materials and applications in this type of industry.
Applications:
- Welding parts for industrial machinery.
- Fabricating appliances such as refrigerators and stoves.
- Joining components for consumer electronics.
Construction and Infrastructure Industry
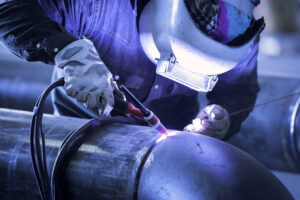
The construction sector is one of the largest consumers of welding services. Welders in construction work on projects ranging from skyscrapers to bridges, ensuring the structural integrity of these monumental buildings.
Applications:
- Welding structural steel beams.
- Joining metal pipes for plumbing and HVAC systems.
- Repairing and maintaining infrastructure.
Oil & Gas Industry
In the oil and gas sector, welding is crucial for constructing pipelines, refineries, and offshore platforms. These structures must withstand corrosive environments and extreme weather conditions.
Applications:
- Welding pipelines for transporting oil and gas.
- Fabricating storage tanks and pressure vessels.
- Repairing and maintaining offshore platforms.
Common welding processes | Benefits | |
Aerospace | TIG Welding (GTAW)
Laser Beam Welding |
Offers exceptional control overheat input and produces clean, precise welds.
Used for joining intricate components with minimal heat-affected zones. |
Railway | Thermit Welding
Flash Butt Welding |
Ideal for welding rails in situ, minimizing disruptions to railway operations.
Commonly used to join rails together seamlessly. |
Automotive | Resistance Spot Welding
Robotic Welding |
Used for joining sheet metal parts quickly.
Automated systems for high-volume production, ensuring consistent weld quality. |
Manufacturing | Gas Metal Arc Welding (GMAW)
Spot Welding |
Versatile and suitable for various materials like steel, aluminum, and stainless steel.
Efficient for joining sheet metal components in mass production. |
Construction | Stick Welding (SMAW)
MIG Welding (GMAW) |
Common for on-site welding due to its versatility and ability to work in various weather conditions.
Ideal for fast, efficient welding on steel structures. |
Oil & Gas | Flux-Cored Arc Welding (FCAW)
Submerged Arc Welding (SAW) |
Ideal for welding thick materials and in outdoor environments.
Efficient for welding long seams in pipelines. |
The actual situation of the Welding Industry
One of the current concerns in the welding industry is the shortage of qualified welders. This shortage has been a persistent problem for several years and continues to affect several sectors that rely heavily on welding.
Global shortage of welders |
|
Causes |
Impacts |
Aging Workforce: Many experienced welders are nearing retirement age, creating a gap in the industry as younger workers have not filled these positions at a sufficient rate.
Lack of New Entrants: Due to various factors such as a focus on four-year college degrees over technical training, misconceptions about the industry, and limited vocational training opportunities in some areas. Skills Gap: As technology advances and welding techniques become more sophisticated, there is a growing gap between the skills demanded by employers and the skills possessed by available welders. |
Project Delays: The shortage of welders can lead to delays in construction projects, manufacturing timelines, and maintenance schedules. This, in turn, affects overall productivity and profitability.
Quality Concerns: With fewer skilled welders available, there is a risk of compromised weld quality, which can result in safety hazards, rework costs, and reputational damage for companies. Increased Costs: Companies may need to offer higher wages and benefits to attract and retain skilled welders, leading to increased operational costs. Innovation and Technology Adoption: The shortage of skilled welders can hinder the adoption of advanced welding technologies and techniques, as there may not be enough trained personnel to utilize these advancements effectively. |
How to address the Impacts on the Welding Industry?
Efforts to promote welding as a rewarding and viable career option are essential. Highlighting the potential for career advancement, competitive salaries, and job stability can attract more individuals to the field.
There is also a growing need for investment in training programs that bring individuals the necessary welding skills. This includes vocational schools, community colleges, apprenticeship programs, and on-the-job training initiatives. Embracing advanced technologies such as augmented reality (AR), robotic welding, and automation can help offset the shortage by improving efficiency and productivity.
Embracing the New advancements in Welding Technology
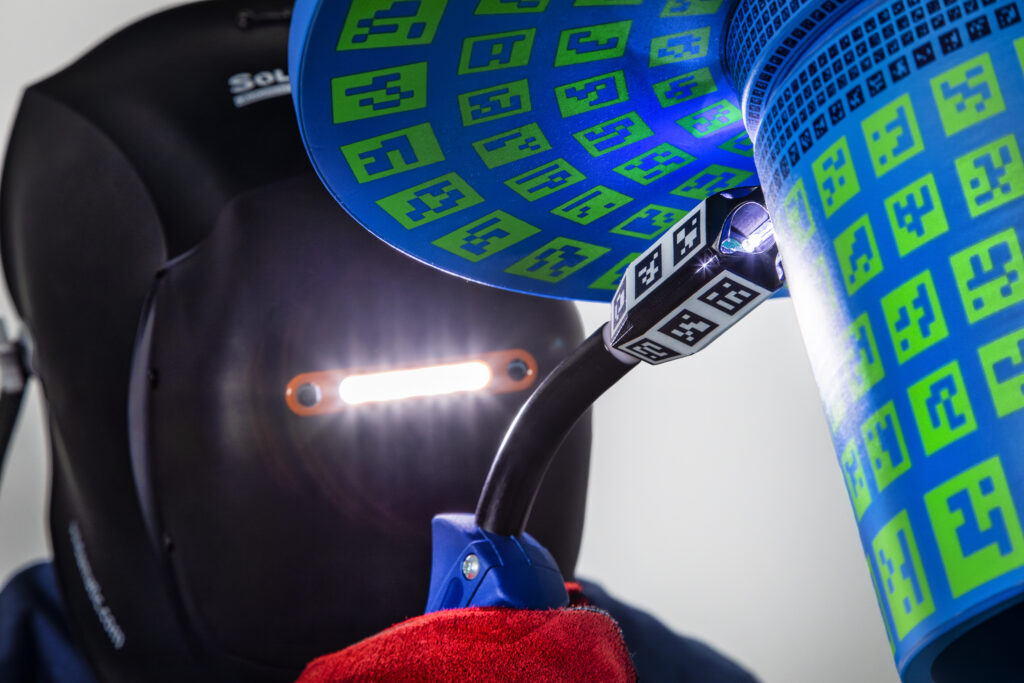
There is a significant relationship between the industries mentioned in this article and training welders using augmented reality technology. AR has revolutionized the way welders are trained by providing immersive, interactive, and efficient learning experiences. As industries continue to evolve with new materials, technologies, and techniques, AR training ensures that welders remain adaptable and ready for upcoming challenges.
Across all these welding industries, Soldamatic offers a boost. Welders can familiarize themselves with safety protocols, potential hazards, and emergency procedures in a controlled, virtual environment. The versatility of AR allows for the integration of new welding methods, materials, and equipment into training modules, keeping welders up to date with industry advancements
It is proven that this welding simulator also accelerates the learning curve for welders by providing immersive, hands-on experiences. Trainees can receive real-time feedback on their welding performance, allowing for immediate adjustments and improvement, while reducing material wastage and fewer errors in production.
Soldamatic can be accessed from anywhere, through the e-learning platform, making it ideal for remote learning and global collaboration. This accessibility also benefits industries with distributed workforces, enabling consistent training standards across multiple sites.
AR in Welding: Training Tomorrow’s Skilled Welders with Soldamatic
Collaboration between industry stakeholders, educational institutions, and government agencies is vital for developing effective training programs that align with industry needs. By taking proactive steps to bridge the skills gap, the welding industry can overcome these challenges and thrive in the future.
As AR technology continues to advance, its role in welding education will only become more essential, shaping a new era of skilled and proficient welders. Soldamatic is the solution for training the welders of the future.