Los defectos de soldadura son, desafortunadamente, más comunes de lo que se piensa. Pueden surgir por una variedad de factores, como técnicas inadecuadas, materiales de baja calidad, o condiciones ambientales adversas. La frecuencia de estos defectos depende de la experiencia del soldador, el equipo utilizado y las especificaciones del proyecto.
Durante el proceso de soldadura pueden producirse irregularidades debidas a técnicas incorrectas, o a una mala relación con la posición de la pieza respecto al soldador, que también pueden comprometer la calidad de la soldadura e impiden la realización de la soldadura de manera adecuada. Cuando una irregularidad o discontinuidad que no supera la norma de homologación o por el contrario supera sus límites, se convierte en un defecto. En este artículo, exploraremos algunos de los defectos de soldadura más comunes y profundizaremos en las razones de su aparición, junto con soluciones prácticas para mitigarlos.
¿Qué es un defecto de soldadura?
Un defecto de soldadura es una imperfección o irregularidad en una unión soldada que se desvía de la calidad o las especificaciones deseadas. Estos defectos pueden comprometer la integridad, resistencia y funcionalidad de la soldadura, lo que puede provocar fallos estructurales o reducir el rendimiento del componente soldado.
Los defectos de soldadura pueden adoptar diversas formas, como grietas, porosidad y otras. Estos problemas pueden surgir debido a una serie de factores, como unos parámetros de soldadura incorrectos, una preparación inadecuada de los materiales, un control de calidad deficiente o factores ambientales. Pero incluso los soldadores más expertos encuentran defectos de vez en cuando.
Para garantizar la fiabilidad y seguridad de las estructuras o componentes soldados, es fundamental detectar y tratar los defectos de soldadura, sus causas profundas y los remedios eficaces. Esto suele hacerse mediante inspección visual, métodos de ensayo no destructivos y acciones correctivas como la recostura de soldaduras, el esmerilado o el tratamiento térmico.
Tipos de defectos de soldadura
En primer lugar, conviene conocer la categorización de los defectos. Según la zona de la soldadura, los defectos pueden ser externos o internos. En relación con su tamaño, forma y orientación, pueden clasificarse como volumétricos o planares.
Defectos externos de soldadura
Estas irregularidades se producen en la superficie de la soldadura; pueden reconocerse mediante inspección visual u otros métodos no destructivos.
- Mordedura. Es un defecto externo caracterizado por un surco o depresión a lo largo del cordón de soldadura, que reduce el espesor del metal base, y el resultado es una pieza débil. Puede deberse a la falta de una buena temperatura durante la cristalización de la unión, o a no aplicar una buena velocidad de desplazamiento. Por otro lado, se produce un solapamiento cuando la soldadura se expande más allá del cordón de soldadura.
- Sobreespesor o refuerzo excesivo. Es un exceso de material depositado en las pasadas finales. Este defecto puede ser el resultado de una corriente extrema, velocidades de desplazamiento excesivamente lentas y un ajuste inadecuado de la junta. Dependiendo de la normativa, se considera sobreespesor si es superior a 3 mm (suele estar en un rango aceptado de 1 a 3 mm).
- Salpicaduras excesivas. Puede describirse como las gotas de metal de soldadura expulsadas durante la soldadura que se adhieren al metal circundante.
Defectos internos de soldadura
Discontinuidades situadas en el interior de la soldadura; no pueden detectarse mediante inspección visual. Además, para reconocer esta irregularidad, muchos tipos de métodos no destructivos tampoco son útiles.
- Embridamiento excesivo. Se produce cuando se aplica una tensión muy elevada a la hora de realizar el punteado de una pieza, generando una tensión interna en el metal, la cual permanece una vez enfriado el material y produciendo grietas. Estas grietas están ocultas en el interior de la unión soldada y a menudo sólo se detectan mediante métodos de ensayo no destructivos, como los rayos X o los ultrasonidos. Pueden ser grietas longitudinales, transversales o en cráter. Estas grietas pueden propagarse a través del material, comprometiendo su resistencia.
- Penetración incompleta. Es un tipo de falta de fusión que ocurre cuando se da en el cordón de penetración o raíz. El metal de soldadura no penetra completamente en el espesor de la junta (no hay una penetración total).
Defectos volumétricos de soldadura
Los defectos volumétricos son defectos tridimensionales que se producen dentro del metal de soldadura o de la zona afectada por el calor (HAZ). Esto significa que se producen dentro de la unión soldada y afectan a su volumen o estructura interior.
- Porosidad. Este defecto se produce cuando quedan atrapadas burbujas de gas en el metal de soldadura durante la solidificación. Afecta a la soldadura reduciendo su sección transversal y puede estar dispersa por toda la soldadura o localizada. Además, es un tipo de defecto que puede darse de manera interna o externa, siendo visible en la superficie de la soldadura o requiriendo de procedimientos de inspección no destructivos para localizarlos, respectivamente. Las burbujas de gas no son visibles en la superficie de la soldadura, pero pueden debilitar su integridad.
- Inclusión de escoria. Se trata de materiales sólidos no metálicos atrapados en el metal de soldadura. Las inclusiones de escoria suelen ser el resultado de no utilizar la técnica de soldadura adecuada, lo que impide que la escoria flote hasta la superficie del baño de soldadura para ser eliminada.
Defectos planos de soldadura
Los defectos de soldadura planos son imperfecciones que se producen a lo largo de la superficie o de un único plano de una unión soldada. Estos defectos suelen ser bidimensionales y son importantes porque pueden comprometer la integridad estructural de la soldadura, lo que puede provocar fallos bajo tensión.
- Falta de fusión. Es una discontinuidad en la soldadura, en la cual no se produce la mezcla del material base y el de aporte, pudiéndose ubicar en capas intermedias de la soldadura y provocando una penetración incompleta.
- Desfondamiento. Se trata de una zona longitudinal continua o intermitente en la superficie de una soldadura que se sitúa por debajo del nivel del metal base circundante, como resultado de una deposición inadecuada del metal de soldadura. Este defecto es visible externamente y puede identificarse mediante inspección visual. Factores como la alta velocidad de desplazamiento de la soldadura y el aporte excesivo de calor son causas comunes de insuficiencia de relleno.
Categorización de los defectos de soldadura |
|||
ÁREA |
FORMA |
||
Defecto externo | Defecto interno | Defecto volumétrico |
Defecto plano |
Sobreespesor | Grietas | Inclusión de escoria | Falta de fusión |
Porosidad | Porosidad | Porosidad | Desfondamiento |
Mordeduras | Penetración incompleta | Solapamiento | Penetración incompleta |
Salpicaduras | Grietas |
Es importante que los soldadores e inspectores comprendan estas clasificaciones, ya que determinan los métodos utilizados para detectar y solucionar los defectos. Los remedios para estos defectos pueden ser el uso de materiales convenientes, la eliminación de impurezas, el uso de un ángulo de electrodo conveniente, o precalentar adecuadamente la soldadura según sea necesario, y aplicar una velocidad de desplazamiento adecuada durante el proceso.
Ejemplos de soluciones para defectos de soldadura |
|
Mordedura |
|
Porosidad |
|
Fusión incompleta |
|
Grieta de soldadura |
|
Aprovechar la tecnología de realidad aumentada
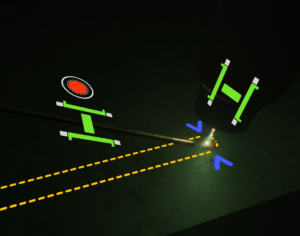
¿Sabes que Soldamatic puede habilitar guías durante la práctica? Este simulador de soldadura que funciona con RA analiza tus movimientos durante el ejercicio, proporcionando feedback instantáneo y haciéndolo más instructivo. El soldador puede observar en tiempo real si el ángulo, la velocidad de desplazamiento, la intensidad o el voltaje no son los convenientes, ya que aparecen señales rojas durante la simulación. Por otro lado, las guías aparecerán en verde si la práctica es correcta.
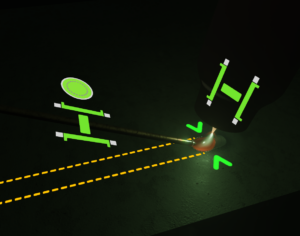
Además, se puede mejorar la memoria muscular sin desperdiciar materias primas acero al carbono, aluminio o acero inoxidable. Garantizar unas técnicas de soldadura adecuadas y evitar los errores de soldadura habituales también es esencial para el control de las materias primas. La tecnología de realidad aumentada presenta un enfoque muy positivo para mitigar estos costes.
Esta revolucionaria solución ha sido desarrollada para soldadores por soldadores y ofrece numerosas ventajas en la formación y el desarrollo de habilidades de soldadura. Soldamatic ofrece diferentes programas de formación certificados por conocidas asociaciones de soldadores en función de sus necesidades específicas. En nuestra sección de casos prácticos puedes consultar las empresas industriales y escuelas de formación profesional que ya están aplicando la Metodología Aumentada.
También puedes crear tu propio ejercicio para evaluar las habilidades de los soldadores. Por ejemplo, Soldamatic e-learning te permite generar una WPS con valores erróneos desde el principio. De este modo, si inician el cordón de soldadura, la propia simulación muestra los defectos durante la ejecución. También pueden analizar el cordón de soldadura en el módulo de análisis que aparece justo después de la práctica.
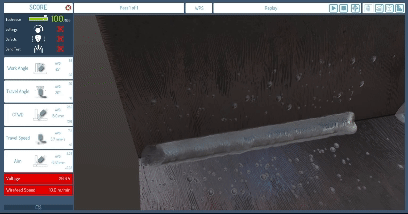
34%
más soldadores cualificados que con la metodología tradicional
56%
reducción del tiempo real de aprendizaje
68%
de reducción de los costes del taller
84%
menos accidentes
Un enfoque transformador para mitigar los Defectos de Soldadura
Los accidentes de soldadura se producen cuando se descuidan las precauciones. Los defectos internos suelen requerir técnicas de inspección más avanzadas, como pruebas ultrasónicas o radiografías, mientras que los defectos externos pueden identificarse a menudo mediante inspección visual. Los remedios para estos defectos pueden consistir en eliminar impurezas, utilizar un ángulo de electrodo conveniente o aplicar una velocidad de desplazamiento adecuada durante el proceso. Al comprender las causas fundamentales de estos defectos de soldadura comunes y aplicar remedios eficaces, los soldadores pueden mejorar la calidad, resistencia y fiabilidad de sus soldaduras.
La formación continua, el cumplimiento de las mejores prácticas de soldadura y la atención a los detalles son esenciales para minimizar los defectos y lograr una calidad de soldadura superior en diversas aplicaciones industriales. Los sistemas de RA permiten a los soldadores trabajar con mayor precisión y eficacia, al tiempo que fomentan la seguridad, la productividad y la rentabilidad. Soldamatic es la solución para enfatizar las mejores prácticas y la prevención de errores.