People are so used to welding, that sometimes they forget the importance the welding industry has in our daily lives. It is an essential part of our lives, from our means of transport to our buildings, but furthermore, to almost every industry, welding has a transverse role.
However, the trade is living fast changes, and it needs to adapt to new generations. According to the American Welding Society (AWS), the average age of a welder is in the mid-fifties, and many are approaching 60 years old. These experienced workers are close to their retirement, and the problem is growing with the lack of incoming skilled workers.
The AWS estimates the US will face a shortage of 400.000 skilled welders by 2024, in an industry valued at more than $5.5 billion, the problem is real, and given the transversal role of the trade, it will grow even bigger.
The lack of skilled welders is starting to have its effects on different industries, in 2018 both Fiat and Ford experienced trouble with their cars due to welding issues. Fiat had to recall 18000 Jeep Wranglers because of a faulty weld in the frame of the vehicle. The defective pump welds in some of their vehicles forced another automotive giant, Ford, to recall 12000 vehicles in North America. This kind of welding issues are also having an impact on other industries, the UK had to delay their new £31 billion nuclear missiles when it was discovered that the missile tube had cracks.
It is clear that the welding industry is living difficult times, what makes new changes and trends necessary. The trade needs to be appealing to newcomers, and the need of skilled workers can and should be a motivation call for people looking for a career. So, what should be the next move in the welding industry? How can it face its problems?
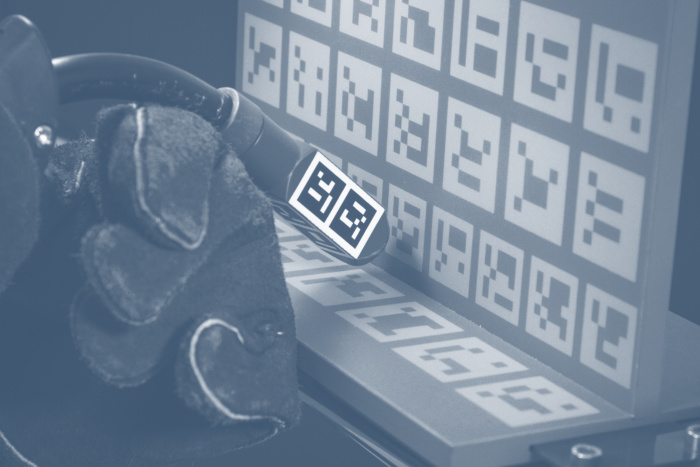
The solution must go through new tecnologies and methodologies, able to disrupt traditional methods and bring the welding industry to the next level. This goal can be achieved in different ways, one of them is applying one of the biggest technological trends in the world, Augmented Reality (AR) to welding training.
The AR technology can provide motivation to newcomers, providing them individualized and experimental learning, therefore fostering their learning process. From the trainer’s point of view, it means savings and a complete reduction of accidents, more frequent in beginners. To sum up, Augmented Reality is the perfect tool to attract, develop and empower the current and next generation of the industrial labour.
The mix of Augmented Reality and welding training is already growing around the world, thanks to Soldamatic Augmented Training, the first welding simulator powered with AR. It is already available in more than 50 countries, and industrial leaders such as Volkswagen, John Deere, Man or Siemens are already applying it to qualify better welders.
Sources: