Welding joints, techniques and expertise are applied to countless industries, from automotive and aeronautical, to manufacturing and shipping. Welders are required to have versatile knowledge about the different types of welds and how to perform them, even when the welding required is not as comfortable as hoped.
Being adept at handling different welds and joints is part of the toolkit of any great welder, but what are they and how do they differ? In this article, we are going to explore and explain.
What is welding?
Let’s clarify this first, before we process. Welding is the process of joining two pieces of a material (in this case, metal) together using heat. A weld is formed to join points or edges, based on the shape of the materials. As you can imagine, there are only a few different ways that two things can be welded together. All of the various combinations of angles and techniques are grouped into these fives terms:
- Tee Joint
- Edge Joint
- Corner Joint
- Lap Joint
- Butt Joint
Let’s look into each of these in more detail…
Tee Joint
As you can imagine, a Tee Joint is shaped like the letter T, with two pieces of metal being welded to intersect at a 90° angle. The edge is joined to a plate or a component, with extra care being taken to ensure effective penetration into the roof of the weld.
A Tee Joint is a type of fillet joint (we’ll talk about these later), and there are several different welding styles used to create Tee Joints:
- Fillet Weld
- Plug Weld
- Bevel-Groove Weld
- Slot Weld
- J-Groove Weld
- Melt-Through Weld
- Fare-Bevel-Groove Weld
If the base metal is thick and after welding on both sides it still cannot support the load, it is in this case that a groove-type weld will be applied.
Tee Joints are not perfect, as they are known to suffer from Lamellar Tearing. This is when too much pressure on the solid and inflexible joint causes it to crack. A stopper can sometimes be used to prevent this, or the base metal quality can be improved.
Edge Joint
This is the most common form of welding for sheet metal, especially where there are flanged edges (curved). It’s also a popular weld choice for connecting metal to adjacent pieces, so if you imagine you have two quarter-pieces of a pipe and you want to weld them side by side. Instead of welding the space between them, you weld the top edge surface where the two adjacent pieces meet. This type of weld helps to manage the stresses that the metal will face, though depending on the application of the metal, it may be worth adding filler metal for reinforcement.
Some of the stresses include:
- Tensile
- Compression
- Bending
- Torsion
- Shear
Some joints can handle forces better than others and it’s these considerations that allow the welder to make their decision.
Some of the welding styles used to create edge joints include:
- Square-Groove Weld
- Butt Weld
- J-Groove Weld
- Bevel-Groove Weld
- V-Groove Weld
- U-Groove Weld
- Edge-Flange Weld
- Corner-Flange Weld
Corner Joint
Like the Edge Joint, this is one of the most popular methods of welding sheet metal and is applied where two pieces join at their outer edges to form a corner. The edges come together at right angles to form an L shape and are commonly used for welding boxes and frames.
This is not one of the strongest welds, as the two pieces of metal are quite exposed to bending and misalignment, especially when the metal is quite thin or flexible. One way to shore up the weld is to make sure the joint is welded on all sides and is not left as a single-side weld. Filler metal can also be used, but it’s advised to use only a small amount, and with less thickness than the base metals.
These welding styles can be applied to do a Corner Joint:
- Spot Weld
- V-Groove Weld
- Fillet Weld
- U-Groove Weld
- Bevel-Groove Weld
- Square-Groove Weld
- Butt Weld
- Flare-V-Groove Weld
- Corner-Flange Weld
- Edge Weld
- J-Groove Weld
You may have noticed that a Tee Joint and a Corner Joint are very similar, and it’s true. What separates them is the location of the weld, with Tee Joints being placed in the middle to effectively creating two right angles.
Lap Joint
The Lap Joint is commonly applied to the welding of two pieces of metal that are of different thicknesses. Some might say that this type of joint would be better being called an ‘Overlap Joint’, as the name is derived from how the two pieces of overlapping metal are welded.
When the two pieces of metal are overlapped, this presents two sections to be welded to give added strength to the joint. It’s advised that both of these corners are welding to give the weld the best chances.
Some of the welding styles for Lap Joints include:
- Plug Weld
- Slot Weld
- Spot Weld
- J-Groove Weld
- Bevel-Groove Weld
- Flare-Bevel-Groove Weld
Butt Joint
Our fifth and final welding joint is the Butt Joint, perhaps the most common, affordable, and straightforward type of weld. Two pieces of metal are placed end-to-end or side-by-side and are welded where the edges meet. This same theory works for flat metal and pipes, as long as the edges that are being welded correspond.
Some might refer to the Butt Joint as a ‘Square-Groove Weld’, and beyond flat metals and pipes, they could use it to join flanges, valves, fittings, and essentially any parallel pieces of metal.
This is the welding style that most beginners learn first, and it can be used for:
- Square-Groove Butt Welds
- V-Groove Butt Welds
- U-Groove Butt Welds
- J-Groove Butt Welds
- Flare-V-Groove Butt Welds
- Bevel-Groove Butt Welds
- Flare-Bevel-Groove Butt Welds
Fillet Joints
One word that has popped up a few times in this article, and is used very commonly in the welding industry, is ‘fillet’. This is simply a group term that contains Corner, Tee, and Lap Joints, and accounts for the majority of all welds. Fillet Joints require little preparation, are better for welding pipes, and offer the welder lower costs than Butt Welding. Essentially, a Butt Joint uses filler or excess material between the edges being welded, whereas Fillet Joints use the filler material in the corners to create extra strength.
In the following infographic you can take a look at these 5 welding joints to find out how they look:
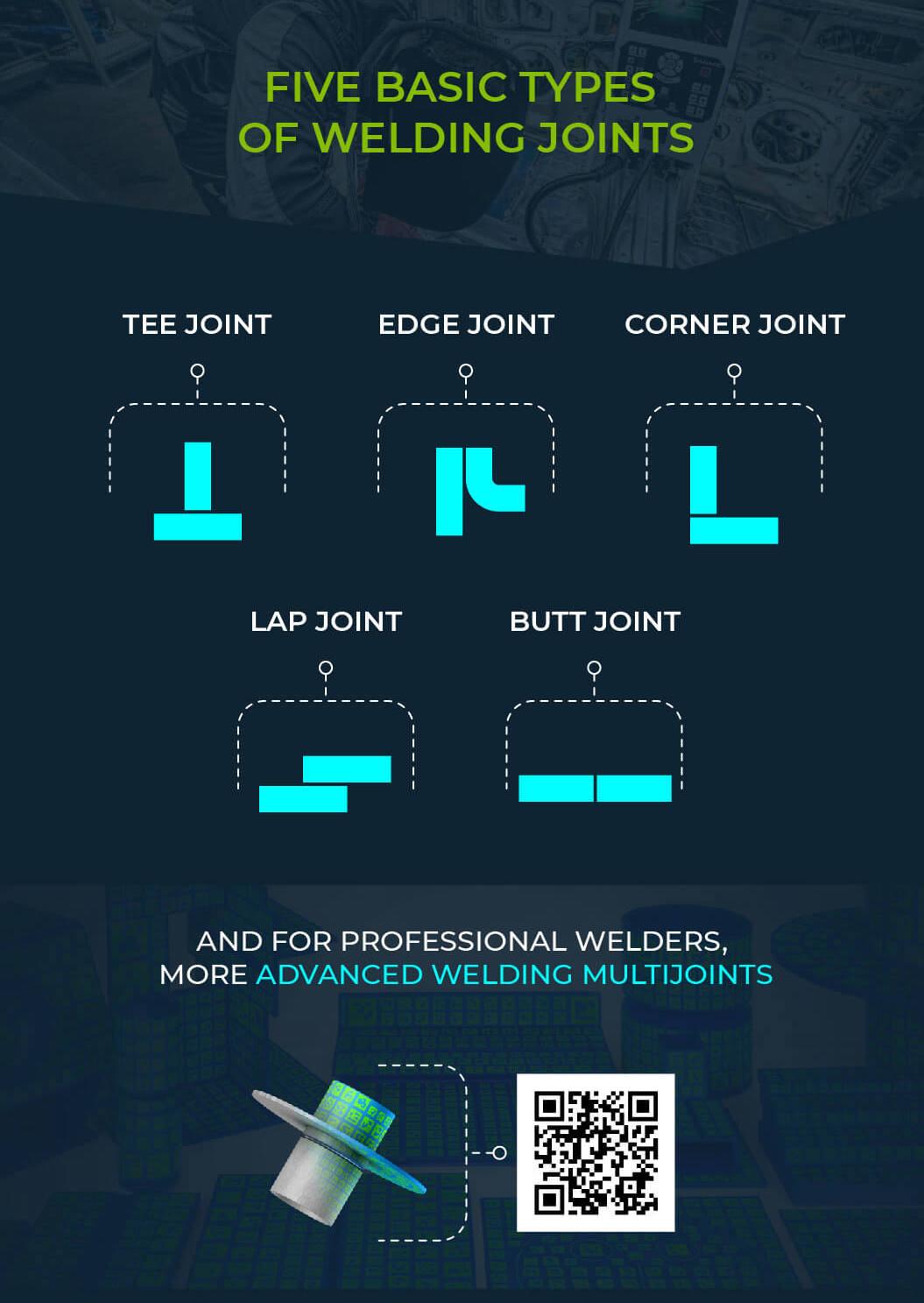
These are the top 5 five basic types of welding joints that every newcomer to the trade should know, but professional welders need to be familiar with more advanced, specific a complex welding joints. These Advanced Welding Joints vary depending on the sector the welder is working at, for example, the Automotive industry tends to use Aluminum whereas the Aerospace Industry uses the TIG process for high-strength titanium joints.
Soldamatic offers the possibility to train not only newcomers, but professional welders with an extensive catalogue with 15 Advanced Welding Multijoints, you can review them in 3D here.
It even offers the possibility to bring real welding joints to Augmented Reality, allowing companies to train their welders in their specific welding joints, materials, positions… while reducing costs and risks. Contact us if you would like to know more about Industrial Welding Multijoints.